Turboréacteur

Le turboréacteur est un système de propulsion qui transforme l'énergie potentielle contenue dans un carburant, associé à un comburant qu'est l'air ambiant, en énergie cinétique permettant de générer une force de réaction en milieu élastique dans le sens opposé à l'éjection.
Ce type de moteur est essentiellement utilisé sur les avions de type commercial ou militaire. La poussée générée résulte de l'accélération d'une certaine quantité d'air entre l'entrée (buse d'entrée d'air) et la sortie (tuyère d'éjection).
Afin d'éjecter une quantité d'air suffisante en masse, un accroissement de la pression à vitesse à peu près constante est assuré par le compresseur d'entrée. Un important dégagement d'énergie est ensuite provoqué par la combustion d'un carburant, généralement du kérosène, dans l'oxygène de l'air qui traverse la machine. Une partie de l'énergie produite est récupérée par une turbine à gaz à la sortie de la chambre de combustion pour entraîner certains accessoires dont le compresseur situé juste en aval de l'entrée d'air, l'autre partie du flux chaud (additionnée ou non au flux froid suivant le type de réacteur) produit la poussée par détente dans la tuyère d'éjection.
Généralités

Depuis le milieu du XXe siècle, le rapport coût/efficacité du turboréacteur le rend particulièrement attractif pour les avions de transport qui volent dans le domaine du haut subsonique (0,7 < Mach < 0,9), d'où son utilisation sur les avions civils des familles Airbus A3xx, Boeing B7xx, etc.
Grâce à des adaptations sur les buses d'entrée pour absorber les ondes de choc en vol supersonique et à une capacité de générer des vitesses d'éjection supérieures à la vitesse du son grâce à une réchauffe des gaz par postcombustion, ils sont capables de couvrir les domaines de vol allant du subsonique au supersonique. Ils sont utilisés par exemple sur les avions de combat (Dassault Rafale, F-16 Fighting Falcon…).
L'industrie du turboréacteur est un secteur majeur de l'aéronautique civile et militaire, ce qui en fait un facteur important de développement technologique et un moteur économique puissant pour un nombre important d'entreprises industrielles et commerciales. C'est une technologie de pointe qui est au carrefour de développements importants dans des domaines aussi variés que la métallurgie, l'électronique, l'informatique, la sûreté de fonctionnement, etc., et par voie de conséquence une grande utilisatrice de recherche appliquée. C'est aussi indirectement en France un facteur d'autonomie dans le domaine de la défense.
Historique
Préambule avant la Seconde Guerre mondiale : les pionniers



Le premier turboréacteur est construit et présenté comme « turbo-propulseur » par le roumain Henri Coanda au salon de l'aéronautique en 1910. Lors d'un essai au sol, son inventeur et pilote, surpris par sa puissance, coupe le moteur, mais l'inertie, bien plus importante que celle d'un moteur à hélice, fait que l'avion décolle quand même, puis, privé de propulsion, atterrit brutalement et brûle partiellement. Coanda revient à une motorisation à hélice mais poursuit ses études et son aventure sera à l'origine de la découverte de l'effet Coanda.
Le moteur Coanda inspire d'abord le français Maxime Guillaume qui est le premier à déposer, le , un brevet d'invention[1] concernant la « propulsion par réaction sur l'air », brevet qu'il obtient le [2]. Néanmoins, il ne sera suivi d'aucune construction, car elle aurait nécessité d'importantes avancées techniques sur les compresseurs et les matériaux.
Dans les années 1930, de nouveaux turboréacteurs sont conçus, à peu près simultanément mais indépendamment, par Frank Whittle en Angleterre et par Hans von Ohain en Allemagne. Whittle, ingénieur aéronautique, s'engage dans la Royal Air Force en 1928 et effectue ses premiers vols en tant que pilote en 1931. Âgé alors de 22 ans, il imagine pour la première fois un avion propulsé sans hélices et essaie sans succès d'obtenir un soutien financier de l'armée pour le développement de son idée[3],[4]. Il persiste alors seul dans le développement de cette motorisation et imagine l'utilisation de deux turbines, l'une à l'entrée pour amener l'air vers la chambre de combustion et l'autre pour mélanger le carburant à l'air[3].

En 1935, grâce à des dons privés, il construit le premier prototype de turboréacteur et le teste au banc d'essai en avril 1937. Le W.1, premier turboréacteur destiné à un petit avion expérimental, est livré le à la société Power Jets Ltd., avec laquelle Whittle est associé. En février 1940, la Gloster Aircraft Company est choisie pour développer un avion mû par le W.1. Le « Pioneer » effectue ainsi son premier vol le [4].
Von Ohain est doctorant en physique à l'Université de Göttingen en Allemagne. Constructeur d'avions, Ernst Heinkel fait appel à l'université pour développer un nouveau type de propulsion aéronautique[3],[4]. Répondant à l'appel, Von Ohain conçoit l'idée d'un moteur dont la combustion se fait selon un cycle continu et dépose en 1934 un brevet de moteur à propulsion similaire à celui de Whittle sur le dessin mais différent sur les éléments internes au moteur. Von Ohain fait voler le premier turboréacteur sur un Heinkel He 178 en 1939, premier aéronef conçu pour être propulsé par ce type de moteurs[4].
Autour de la Seconde Guerre mondiale

Les premiers turboréacteurs dessinés par Whittle et Von Ohain sont conçus sur la technologie des compresseurs centrifuges. Ces turboréacteurs présentent l'inconvénient de nécessiter un moteur de grand diamètre pour pouvoir comprimer correctement l'air à l'entrée du turboréacteur. En 1940, Anselm Franz (en) développe un turboréacteur fondé sur le principe des compresseurs axiaux, dont la section frontale est beaucoup plus restreinte et le rendement meilleur. Le Junkers Jumo 004 devient ainsi en 1944 non seulement le premier turboréacteur moderne mais également le premier produit en série[5],[6].
Les premiers avions à turboréacteurs construits en série sont des chasseurs-bombardiers, tels que les Messerschmitt Me 262 Schwalbe mus par des Jumo 004A, utilisés à la fin de la Seconde Guerre mondiale[6]. Leur conception est facilitée par la forme allongée et le petit diamètre des turboréacteurs axiaux. Après guerre, les turboréacteurs se généralisent, aussi bien dans l'aviation militaire que civile, ainsi que les turbopropulseurs, conçus sur une technologie très similaire, pour entraîner des hélices. Les Alliés construisent un nombre important de nouveaux turboréacteurs, dont « le Me P.1101 (en) est sûrement le plus avancé[7] ».

Ces premiers chasseurs seront néanmoins marqués par un manque cruel de puissance. Le Bell P-59 Airacomet, premier avion de chasse à réaction conçu aux États-Unis, n'a d'ailleurs jamais été engagé dans des missions de combat en raison de ses performances décevantes (sous motorisé, peu manœuvrable à basse vitesse…)[8]. Ainsi, dès 1945, les premiers aéronefs « hybrides » font leur apparition. Ces appareils, à l'image du Ryan FR Fireball, sont en effet mus par un turboréacteur et un moteur à pistons[9]. Par ailleurs, la recherche de vitesses toujours plus importantes sera à l'origine dans les années 1960 d'une nouvelle hybridation : un turboréacteur associé à un statoréacteur. Le Nord 1500 Griffon II fonctionne sur ce principe. Le turboréacteur fonctionne au décollage tandis que le statoréacteur prend le relais en croisière[10].
Par la suite, le développement continu des turboréacteurs devient un enjeu majeur aussi bien militaire (du point de vue de la défense, de l'attaque et de la force de dissuasion) que civil. Conçu par McDonnell Douglas, le F-4 Phantom II est l'un des avions militaires américains les plus importants du XXe siècle et l'avion de combat occidental ayant été le plus produit depuis la guerre de Corée. Mû par deux réacteurs General Electric J79, il est l'un des très rares avions à être réputé pour sa durée de vie et ses aptitudes en mission[11]. D'un point de vue civil, le De Havilland Comet est le premier avion commercial propulsé par des turboréacteurs. Lancé en 1949, il est resté célèbre pour une série d'accidents en plein vol qui a mis en évidence le phénomène de fatigue des structures dans l'aéronautique[12].
1950 – 1980 : la recherche de performances

La recherche de performances plus élevées du point de vue de la poussée se concentre essentiellement sur deux voies : l'augmentation du taux de compression — les compresseurs centrifuges et les premiers compresseurs axiaux atteignent difficilement un rapport de 6 — et l'augmentation de la température d'éjection. Aux États-Unis, en 1953, General Electric développe le J79, dont le compresseur comporte 17 étages, 6 des stators étant à incidence variable. Ce dernier sera produit en 16 500 exemplaires. En 1949, Pratt & Whitney développe le premier réacteur double corps qui amènera au développement du J57 militaire utilisé sur les Boeing B-52 et KC-135, ainsi que les Douglas Skywarrior.
Dans le domaine civil, sous la dénomination JT3C, il sera le propulseur originel des Boeing 707 et Douglas DC-8 et sera, au total, produit à 21 200 exemplaires. Au Royaume-Uni, Bristol développe à partir de 1949 l'Olympus, de technologie similaire. Initialement, il fournira une poussée de 5 000 daN portée vers 6 000 en 1957, près de 8 000 en 1960 et finalement 9 000 daN. Équipé de la postcombustion, il deviendra le propulseur du Concorde avec une poussée nominale de 17 240 daN.
En France, la Snecma développe la série des Atar, qui culminera avec le 9C à 6 400 daN, et équipera les Mirage III et 5. Enfin, l'URSS produit les Mikulin AM-5, AM-9 et RD-9 qui équipent les chasseurs MiG-19 et Yak-25. Les bombardiers Tu-16 et le transport civil Tu-104 sont équipés de l'AM-3 (en) développé par Mikouline qui, bien qu'utilisant la technologie monocorps, atteint près de 10 000 daN.
Le choc pétrolier

En dehors du Concorde, supersonique, les avions commerciaux sont limités à des vitesses subsoniques. L'augmentation de la poussée n'est donc nécessaire que pour propulser des avions de plus en plus lourds. Après le choc pétrolier, les recherches portent sur des moteurs dont la consommation spécifique — le rapport entre la consommation de carburant et la poussée obtenue — est la plus faible possible. La concurrence se révèle très forte entre les trois principaux motoristes — Rolls-Royce au Royaume-Uni, Pratt & Whitney aux États-Unis et CFM, consortium entre l'américain General Electric et le français Snecma — et ceci d'autant plus que Boeing ou Airbus laissent aux compagnies aériennes le choix du propulseur. Les développements portent donc essentiellement sur un nouveau type de turboréacteur, le turbofan ou turboréacteur à double flux, qui peut être considéré comme intermédiaire entre le turboréacteur et le turbopropulseur (voir Propulsion des aéronefs). Le premier développement est réalisé par Rolls-Royce avec le Conway (en) et un taux de dilution initial de 0,3 porté par la suite à 0,6.
La première génération de turboréacteurs à double flux à haut taux de dilution et non développés à partir d'éléments pré-existants a permis d'équiper les Lockheed C-5 Galaxy de l'US Air Force avec le General Electric TF39 (en), qui atteignait une poussée de 19 000 daN. Ce réacteur est à l'origine du CF6, modèle civil qui se retrouve sur les DC-10, Airbus A300 et Boeing 747. Les deux concurrents Pratt & Whitney et Rolls-Royce suivirent avec les JT9D et RB.211, aux performances équivalentes.
Trinôme avion, réacteur, mission
L'avion et la mission sont les dénominateurs communs du développement d'une famille de turboréacteurs. Pour un même modèle d'avion, plusieurs constructeurs peuvent développer des moteurs de même gamme et se répartir ainsi le marché de la gamme.
Les critères avion pris en compte en premier lieu sont :
- le nombre de passagers à transporter ;
- la distance franchissable ;
- la charge marchande ;
- la masse maxi au décollage ;
- la masse à vide ;
- le volume de carburant ;
- le nombre de Mach en croisière ;
- l'altitude de croisière ;
- la surface alaire.
Les types de mission envisagées pour le transport civil peuvent être les suivantes :
- court courrier R < 1 500 NM (Europe domestique) ;
- court moyen courrier 1 500 NM < R < 3 000 NM (États-Unis domestique) ;
- moyen courrier 3 000 NM < R < 4 500 NM (Europe - Afrique) ;
- long courrier 4 500 NM < R < 6 000 NM (Europe - États-Unis) ;
- très long courrier 6 000 NM < R (Europe - Asie et États-Unis - Asie).
R étant le rayon d'action et 1 NM (mille marin) = 1,852 km
Pour les opérations militaires, les durées de vol peuvent varier entre 40 min et plusieurs heures en cas de vol avec bidons ou ravitaillement en vol.
Le profil type d'une mission pour le transport civil peut se décomposer en phases successives telles que :
- Taxi ;
- Take-Off to 35 ft ;
- Climb and Accel 1 500 ft - 250 kt ;
- Climb 250 kt ;
- Accel to climb speed ;
- Climb ;
- Step cruise (limit 40 000 ft) ;
- Descent ;
- Deccel to 250 kt ;
- Deccel at 250 kt ;
- Approach and Landing ;
- Taxi.
Le dimensionnement du turboréacteur est donc la synthèse de tous ces critères objectifs et demande donc une étude très approfondie des besoins du client.
Les grands dilemmes de l'aéronautique
Pour répondre aux besoins du client, le motoriste doit développer un moteur qui soit :
- Léger mais solide afin
- d'augmenter la charge marchande
- de réduire la masse de carburant à emporter
- de permettre des poussées de plusieurs dizaines de tonnes avec des moteurs de seulement quelques tonnes de masse individuelle
- d'avoir des composants résistants à des efforts de centaines de tonnes pour un poids de seulement quelques centaines de kilogrammes
- Sûr et fiable
- Une panne de fonctionnement au plus toutes les 300 000 h
- Une remise en état toutes les 15 000 h
- Compétitif commercialement
- Silencieux et peu polluant
- Maintenance peu coûteuse
- prix du kg transporté le plus faible possible
Technicité et complexité accrues des moteurs

Les turboréacteurs d'aujourd'hui sont des machines d'une extrême complexité regroupant un grand nombre de sous-systèmes. Le développement d'un nouveau moteur demande des moyens humains, technologiques et financiers considérables que seules quelques rares entreprises possèdent dans le monde : General Electric, Snecma, Rolls-Royce, Pratt & Whitney et NPO Saturn pour les plus importants. Les turboréacteurs sont utilisés sur tous les avions civils moyen et gros porteurs, car ils sont les seuls à pouvoir atteindre des vitesses transsoniques (entre mach 0,8 et mach 1) de manière économique[13]. Seuls les petits avions de tourisme et les ULM sont encore équipés de moteurs à explosion à pistons.
La fabrication et l'exploitation d'un turboréacteur nécessitent des connaissances techniques parmi les plus pointues de notre époque telles que la mécanique des fluides, la thermodynamique, la science des matériaux, l'automatique ou encore l'acoustique. D'ailleurs, à bord d'un avion, civil ou militaire, le turboréacteur n'est pas seulement un organe propulsif. Il fournit aussi toute l'énergie disponible à bord sous forme électrique, hydraulique et pneumatique et alimente le système de pressurisation et de conditionnement d'air. Le groupe moteur est ainsi souvent appelé « générateur de puissance » ou « powerplant ». Si le rendement et la fiabilité de ces moteurs se sont considérablement améliorés depuis leurs débuts, leur coût est très important, et représente en général pour un avion civil le tiers du coût total de l'appareil.[réf. nécessaire]
Technique


Préambule
Jusqu'à ces dernières décennies l'hélice avait le monopole de la propulsion des avions mais les phénomènes soniques en limitant l'utilisation à une vitesse inférieure à 720 km/h, soit 200 m/s, il a fallu innover et la deuxième guerre mondiale a accéléré le développement d'un nouveau système de propulsion sans changer le principe initial fondé sur le principe d'action-réaction réalisé dans le milieu élastique qu'est l'air ambiant.
Ce nouveau système peut être considéré comme un tube dans lequel l'air entre à la vitesse V0 et en sort à la vitesse V1 plus grande que V0. De ce point de vue le réacteur ne se distingue pas des hélices sauf par le fait que, lors de la traversée du réacteur, l'air est comprimé et voit donc sa température croître significativement avant d'arriver dans la chambre de combustion. Une deuxième différence avec l'hélice est que l'air est guidé par des parois et cela rend possible l'éjection à des vitesses supersoniques. La dernière différence fondamentale avec l'hélice, qui n'apporte à l'air propulsif une énergie de vitesse que par l'action mécanique de ses pales, tient au fait que dans le réacteur la vitesse d'éjection est obtenue par combustion d'un carburant (Kérosène) injecté dans l'air propulsif et qui, principalement pour un simple flux, permet un accroissement brusque de volume à pression quasi constante dans la chambre de combustion.
Pour un moteur thermique et une hélice l'air servant à la combustion et l'air propulsif sont dissociés alors que pour un réacteur l'air lié à la combustion et l'air propulsif sont partiellement (double flux) ou totalement confondus (simple flux). Malgré cela la vitesse d'éjection des réacteurs comme celle des hélices possède une limite dite « limite métallurgique » que l'on peut situer dans les années 1980 à 3 500 km/h.
Fonctionnement général
Un turboréacteur fonctionne comme le propulseur à hélice sur le principe d'action-réaction réalisé dans le milieu élastique qu'est l'air ambiant et qui fournit une poussée vers l'avant en réaction à l'éjection d'une masse de gaz animée d'une certaine vitesse.
Cette poussée est la conséquence :
- d'une différence de quantité de mouvement entre l'air admis et les gaz éjectés par unité de temps ;
- d'une différence de pression entre le plan de sortie de la tuyère et l'infini amont.
Cette poussée en réaction engendre le déplacement vers l'avant du moteur (d'où le terme moteur à réaction), donc du véhicule sur lequel il est fixé[14].
Principe fondamental
Une masse d'air importante entrant dans le réacteur à une vitesse V1 et en sortant à une vitesse V2 telle que V2 >> V1 produit une force de réaction utilisée comme force de poussée propulsive.
L'admission de l'air servant à la propulsion se fait à travers la Buse d'entrée qui peut être à géométrie variable sur certains avions afin de permettre le vol supersonique.
Aspiré par le Fan puis comprimé via un compresseur axial (ou centrifuge sur certains moteurs) l'air est réchauffé et passe en partie (ou en presque totalité) à travers la chambre de combustion où il est mélangé avec du kérosène pulvérisé qui s'enflamme spontanément (fonctionnement nominal).
À la suite de cette combustion, il se produit alors une forte dilatation des gaz brûlés dont une partie, par leur détente dans la turbine, permet l'entrainement du compresseur, du fan et des accessoires nécessaires au fonctionnement du réacteur.
Le reste des gaz brûlés est transformé en énergie de pression derrière la turbine puis en énergie cinétique par effet Venturi dans la tuyère dont la section peut être variable en fonction du domaine de vol (convergente en subsonique ou divergente en supersonique) afin de réaliser la poussée permettant le mouvement de l'avion vers l'avant.
L'écoulement de l'air est maintenu subsonique au sein du réacteur dans tout le domaine de vol et le fonctionnement du réacteur continue tant qu'il y a injection de carburant[14].
Cycle thermodynamique

Le turboréacteur est un moteur :
- thermique ;
- aérobie ;
- constitué autour d'une turbomachine à gaz.
Ce cycle est constitué d'une compression adiabatique réversible, d'une combustion isobare irréversible (le réacteur étant considéré comme un système ouvert), d'une détente adiabatique réversible et d'un refroidissement isobare réversible.
Le cycle thermodynamique du turboréacteur comprend quatre stades où l'air subit des modifications physiques ou chimiques :
- aspiration ;
- compression ;
- combustion ;
- détente / éjection.
Ces quatre phases du cycle thermodynamique s'effectuent simultanément à des endroits différents par opposition aux quatre temps du moteur à explosion qui se réalisent au même endroit (dans le même cylindre) et à des instants différents.
Pour assurer la réalisation de ce cycle le turboréacteur (mono flux) est constitué de deux parties :
- un ensemble compresseur-foyer-turbine qui transforme l'énergie chimique du carburant en énergie potentielle de gaz comprimés et chauds ;
- une tuyère d'éjection qui transforme en vitesse l'énergie de pression fournie par le générateur de gaz.
Diagramme du turboréacteur
Les 4 phases du cycle thermodynamique peuvent être représentées par les diagrammes Pression / Volume et Pression / Température cycle de Brayton qui permettent de voir l'évolution des caractéristiques de l'air traversant le turboréacteur.
À l'image des moteurs d'automobiles, le turboréacteur réalise ainsi un cycle continu à quatre phases — admission, compression, combustion et détente/échappement.

Dans le diagramme Pression / Volume la compression est théoriquement adiabatique et se traduit par une élévation de pression et de température. La puissance nécessaire à l'entrainement du compresseur est fonction de la masse d'air qui le traverse et de l'élévation de température entre l'entrée et la sortie de celui-ci. La combustion est théoriquement isobare mais dans la chambre la pression chute légèrement et la température augmente fortement. La pression dans la chambre n'est pas totalement isobare à cause des pertes de charge. La détente est théoriquement adiabatique mais la pression et la température chutent alors que la vitesse augmente. En réalité l'air n'étant pas un gaz parfait, compression et détente sont dits polytropiques.

Dans le diagramme Pression / Température apparait la surface utile S et la limite de T4. Pour augmenter la surface utile, il faut augmenter le taux de compression P3/P2 ou reculer la limite de température T4 limitée par la résistance en température des matériaux dont elle est constituée.
Poussée du turboréacteur
Préambule

La gamme des différents turboréacteurs est assez vaste, tout comme les valeurs de leur poussée. Dans la gamme des avions de transport civil, le plus petit turboréacteur, le TRS 18-1 de Microturbo (division du groupe Safran), atteint entre 120 et 160 daN, tandis que le plus imposant, le GE90-115B, fabriqué par General Electric, développe plus de 40 000 daN[13],[15]. Pour ce qui est des avions de combat, la gamme est beaucoup plus restreinte. Le Pratt & Whitney F119, l'un des réacteurs les plus puissants dans ce domaine, développe entre 9 800 et 15 600 daN, tandis que le Snecma M88 équipant le Dassault Rafale développe de 5 000 à 7 500 daN[13].
Calcul de la poussée
Le turboréacteur comme tous les moteurs à réaction directe est caractérisé par sa poussée qui résulte principalement de deux causes :
- la différence de quantité de mouvement entre l'air admis et les gaz éjectés pendant l'unité de temps ;
- la force résultant de la différence de pression existant entre la sortie de la tuyère et l'infini amont.
La poussée d'un turboréacteur est donc :
- proportionnelle, en négligeant la masse de carburant injectée, au débit-masse d'air le traversant ;
- une fonction croissante de la vitesse d'éjection des gaz en sortie de tuyère.
Soit :
La différence des quantités de mouvement s'écrit, en négligeant la masse de combustible injecté :

La différence des pressions entre la sortie de tuyère et l'infini amont conduit à écrire :

d'où l'expression de la poussée :

Le terme est suffisamment petit pour être négligé et l'expression réduite de la poussée peut s'exprimer à partir des équations[16] :
La mise en vitesse des gaz se fait dans la tuyère par transformation de l'énergie potentielle de pression totale et de température totale en énergie cinétique à la sortie du col de tuyère. Tant que la tuyère est en régime subsonique la pression statique dans le plan de sortie est égale à la pression ambiante. Si la vitesse des gaz devient supérieure à Mach 1 alors la pression statique au col devient supérieure à la pression ambiante et des ondes de choc se forment en aval (anneaux en sortie de tuyère sur réacteurs en post-combustion).
La vitesse isentropique en sortie de tuyère a pour équation :
![V_{Isentropique}=\sqrt[]{2*Cp*Tt*(1-(\frac{Pamb}{Pt})^\frac{\gamma-1}{\gamma})}](../i/m/f0923412ac0c28df61d1c3767f5f3fa5.png)
avec :
Ainsi, pour que le turboréacteur crée une poussée vers l'avant, il faut que la vitesse des gaz d'échappement soit supérieure à celle de l'aéronef[16].
Une même poussée peut être obtenue avec un débit plus faible et une vitesse d'éjection du gaz plus élevée, ou au contraire, un débit plus élevé à moindre vitesse. Il est cependant plus avantageux de favoriser le débit plutôt que la vitesse dans le cas des vitesses subsoniques.
Puissances et rendements
Il faut distinguer plusieurs niveaux de puissance et donc de rendement dans le fonctionnement du turboréacteur :
La puissance calorifique fournie au turboréacteur à partir de la combustion d'un carburant et qui s'exprime par le produit du débit carburant et de son pouvoir calorifique. C'est la puissance que l'on pourrait extraire du carburant si la machine était parfaite et qui s'exprime par la formule :

avec :
: puissance fournie par le carburant
: rendement théorique du cycle
La puissance thermique communiquée à la masse gazeuse pendant son passage dans la machine et qui s'exprime par la formule :

La puissance cinétique du jet de gaz éjecté à la sortie de la tuyère et qui s'exprime par la formule :
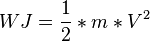
La puissance propulsive qui est la puissance prélevée sur la puissance cinétique des gaz éjectés que l'avion utilise réellement et qui est le produit de la poussée par la "vitesse air" de l'avion

À partir de ces niveaux de puissance on détermine plusieurs niveaux de rendement pour le turboréacteur :
Le rendement thermodynamique (40 %) qui est le rapport de la puissance thermodynamique à l'énergie fournie par le carburant et qui s'exprime par la formule :

Le rendement thermique (30 %) qui est le rapport entre la puissance cinétique du jet de gaz et la puissance calorifique du carburant s'exprime par la formule :

Ce rendement caractérise l'efficacité de la machine à produire de l'énergie potentiellement utilisable pour la propulsion. On améliore ce rendement en augmentant la température du flux sortant de la chambre de combustion en corrélation avec l'augmentation du rapport de compression de l'air en amont de celle-ci. La réduction des pertes de charge et l'augmentation du rendement de l'ensemble turbine participe également à l'augmentation globale de ce rendement.
Le rendement interne (80 %) qui est le rapport de la puissance thermique à la puissance thermodynamique et qui s'exprime par la formule :

Le rendement propulsif qui est le rapport entre la puissance utilisée pour la propulsion et la puissance cinétique du jet (60 % pour une Vi donnée) caractérise la manière dont l'énergie produite par le générateur de gaz est réellement utilisée pour la propulsion. on améliore ce rendement en diminuant la vitesse d'éjection du jet pour l'adapter aux performances de vitesse attendues de l'avion.
Le rendement global (20 % à 25 %) qui est le rapport de l'énergie produite à l'énergie libérée par le carburant et qui peut s'exprimer par la formule :

Carburant, combustion et consommation
Carburant
Les carburants pour turbomachines ont fait leur apparition à la fin de la seconde guerre mondiale. Depuis, l'évolution de leurs spécifications s'est faite en fonction :
- des progrès réalisés dans la technologie des turbomachines ;
- des capacités de production de tel ou tel type de carburant.
Deux caractéristiques principales de température permettent de différentier l'utilisation des différents carburants :
- le point de congélation ;
- le point éclair (inflammation en présence d'une étincelle).
Différents carburants sont employés dans l'aéronautique :
- le Kérosène JET A-1/JET A/JP1 encore appelé TRO utilisé par les militaires, obtenu par distillation directe, dont le point éclair est supérieur à 38 °C et le point de congélation inférieur à −41 °C ;
- le JET B/ JP4 (large coupe) ou TR4 utilisé par les militaires qui sont des produits intermédiaires entre le kérosène et l'essence, obtenus par mélange de kérosène et d'essence, dont le point éclair est compris dans une plage de −25 °C à 15 °C ;
- le JP5 carburant obtenu par distillation directe et avec un point éclair supérieur à 60 °C permettant son utilisation sur les porte-avions pour un maximum de sécurité.
Certains additifs améliorent les qualités de ces carburants tels que :
- antioxydant et désactivants de métaux ;
- inhibiteurs de corrosion ;
- anti-glace ;
- dissipateur d'électricité statique.
Le carburant utilisé dans les turboréacteurs civils et militaires est principalement du kérosène, produit pétrolier obtenu par raffinage des pétroles bruts et composé de carbone à 86% et d'hydrogène à 14 % avec un point éclair pour la sécurité d'utilisation qui se situe aux alentours de 41 °C.
Combustion
La combustion est dans le cas des turboréacteurs une réaction chimique entre un carburant, constitué d'atomes de carbone et d'hydrogène dont la formule générale est CxHy, et un comburant qui est l'air ambiant.
Combustion stœchiométrique
Le mélange carburé est dit stœchiométrique lorsque les constituants sont dans un rapport tel qu'ils participent tous à la combustion. Dans ce cas, les seuls produits de la combustion seront le CO2 et la vapeur d'eau.
La combustion stœchiométrique du kérosène dans de l'air sec a pour équation générale :
CxHy + (x+y/4) (O2 + 3,76N2) → x CO2 + y/2 H2O + 3,76 (x + y/4) N2
Pour x = 10 et y = 20 soit la formulation C10H20, on obtient le bilan massique suivant :
140 kg de kérosène + 2 058 kg d'air sec → 440 kg de dioxyde de carbone + 180 kg de vapeur d'eau + 1 578 kg d'azote.
Ce type de combustion ne se rencontre pas aujourd'hui dans les turboréacteurs et le rapport débit carburant sur débit d'air qui est de 0,068 pour une combustion stœchiométrique est plutôt de 0,03 pour un moteur militaire et 0,02 pour un moteur civil.
Combustion réelle
L'air ne contient pas seulement de l'oxygène mais aussi de l'azote (N2) et des traces de gaz rares (argon, etc.) que l'on retrouve sous forme d'oxydes polluants en fin de combustion. Ces polluants viennent s'ajouter à l'oxyde de carbone (CO) et au carbone (C) sous forme de fumées qui résultent d'une combustion incomplète du carburant.
La combustion n'est possible qu'à partir d'un certain niveau de température et de pression et demande une quantité d'oxygène minimale. Dans la chambre de combustion principale d'un turboréacteur la réaction n'est pas stœchiométrique, c'est une combustion pauvre avec excès d'oxygène et avec présence de vapeur d'eau.
Il reste de l'oxygène dans les produits de combustion de la chambre principale ce qui permet sur les moteurs militaires d'alimenter une post-combustion afin de générer un excédent de poussée à température plus élevée sans crainte de détérioration de pièces tournantes.
Consommation
La consommation en carburant des turboréacteurs qui augmente proportionnellement avec la poussée est évaluée par un paramètre appelé consommation spécifique qui représente le rapport de la consommation de carburant à la poussée obtenue pour un moteur donné.
Les moteurs de dernière génération présentent pour la plupart un ratio de 0,55 en vol de croisière. Cette valeur, pour un Boeing 777 équipé de deux GE90 parcourant 10 000 km à une moyenne de 1 800 L/100 km, équivaut à environ 5 L/100 km par passager (pour 360 passagers), soit autant qu'une petite automobile[13].
Cependant, les petits réacteurs, du fait d'une construction très simplifiée, ont une plus forte consommation spécifique[réf. souhaitée].
Contraintes de fonctionnement

Les turboréacteurs sont des machines de conception très complexe qui doivent supporter des sollicitations thermiques, mécaniques et vibratoires intenses et répondent à de fortes contraintes d'exploitation. Les caractéristiques ne sont pas données de façon précise par les constructeurs mais on peut estimer entre 200 °C et 2 000 °C les températures de fonctionnement[17].
Ces contraintes nécessitent donc des matériaux adaptés à chaque zone. De façon générale, la turbine haute pression est soumise aux conditions les plus sévères (températures et pressions élevées). Les pièces dans cette zone sont en général à base d'alliage de nickel et de cobalt. Dans les zones plus froides, l'acier et le titane sont davantage utilisés[17]. Les surfaces internes, notamment celles des aubes et des carters, sont de surcroît protégées par des revêtements afin d'augmenter la durée de vie des matériaux.
Le développement des turboréacteurs s'est d'ailleurs fait surtout grâce à la maîtrise des matériaux qui composent la conduite des gaz, car ce sont eux les plus fortement sollicités. Cette connaissance des matériaux permet d'obtenir des pièces d'une résistance mécanique maximale pour un poids minimal. Encore aujourd'hui, il s'agit d'une des applications qui demandent la plus haute technicité dans le domaine de la science des matériaux : pièces en titane, aubes en alliage monocristallin, traitements thermiques, etc.
Pollutions générées par les réacteurs
Pollution sonore
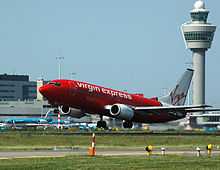
Généralités
Au décollage, le bruit engendré par un turboréacteur est considérable surtout pour les mono-flux et les double-flux avec postcombustion. Le bruit est d'autant plus important que la vitesse d'éjection est élevée ce qui est le cas pour les moteurs équipant les avions de chasse. Le turboréacteur est la principale source de pollution sonore des avions, mais pas la seule. Les volets et les trains d'atterrissage ont un impact non négligeable, au décollage et à l'atterrissage[13]. En outre, même si on estime que moins de 10 % de la gêne acoustique est due aux aéronefs[13], les turboréacteurs, et plus globalement les moteurs d'avions, génèrent des sons de très basses fréquences qui sont mal atténués par la distance et les murs des maisons modernes. Des progrès significatifs ont néanmoins été réalisés depuis 50 ans puisque le niveau sonore des avions a diminué de plus de 10 dB aussi bien au décollage ou à l'approche qu'en vol[13].
Atténuation des nuisances sonores
Le turboréacteur génère deux types de bruits : celui dû à l'éjection des gaz et celui induit par les interactions entre les aubes tournantes et les différents conduits. Le second devient prépondérant sur le premier lors des phases de décollage ou d'approche[18]. Étant donné que le but est de réduire les émissions sonores dans les zones habitées, les études portent donc sur la réduction de ce deuxième type de bruit.
L'un des programmes les plus connus destinés à réduire les émissions sonores des turboréacteurs est le projet européen « Resound » d'absorption acoustique active. Le principe du projet est de créer une onde de même structure spatiale — c'est-à-dire de même fréquence, de même amplitude et possédant la même directivité — que le bruit de raie de la soufflante, mais déphasée de 180°. Pour cela, un mode acoustique identique au mode d'interaction est généré grâce à une grille de contrôle constituée de tiges radiales. Bien que le niveau acoustique des harmoniques soit augmenté à cause de la création de nouveaux sons d'interaction, le gain fondamental atteint 8 dB[18],[19].
D'autres projets plus récents, comme le « LNA-2 » pour Low Noise Aircraft 2, s'intéressent davantage au rayonnement acoustique en aval. Débuté en janvier 2005, le programme s'appuie sur une caractérisation expérimentale et numérique pour réduire les effets de ce rayonnement[20].
Pollution atmosphérique
Généralités

Les émissions polluantes issues de la combustion du kérosène sont l'un des problèmes majeurs du turboréacteur pris « à bras le corps »[13] par les ingénieurs. Néanmoins, ils doivent être relativisés, puisque le trafic aérien ne représente que 5 % des émissions polluantes au voisinage des habitations, et que le CO2 émis ne contribue à l'effet de serre du globe terrestre qu'à hauteur de 2 %. Les effets des traînée de condensation sont essentiellement des cristaux de glace générés par la vapeur d'eau, elle-même produite par la combustion du kérosène et cristallisée par le froid[réf. nécessaire].
Toutefois, la pollution aérienne en haute altitude pourrait avoir bien plus d'impact sur l'environnement et notamment sur l'amincissement de la couche d'ozone. En effet, 75 % des émissions des turboréacteurs ont lieu en vol de croisière dans la troposphère et la basse stratosphère[21].
Produits de combustion
Parmi les produits de combustion liés au fonctionnement des turboréacteurs, on trouve deux gaz toxiques :
- le monoxyde d'azote à haute température ;
- le monoxyde de carbone en fonctionnement au ralenti du moteur.
Les problèmes de combustion à résoudre sont liés aux modes de fonctionnement du turboréacteur suivants :
- au ralenti il faut avoir une richesse élevée pour augmenter la vitesse de réaction du moteur et la température de fonctionnement ;
- au plein gaz il faut réduire la richesse pour baisser la température et obtenir un gain ;
- sur la pollution par les fumées et le monoxyde d'azote,
- sur les températures des parois internes du moteur,
- dans l'homogénéité des températures des gaz d'éjection.
Pour diminuer la pollution on agit sur différents axes au niveau des chambres de combustion :
- une combustion étagée à l'aide de chambre à double têtes ;
- une géométrie interne variable.
Constitution et performances
Le turboréacteur fait partie d'un ensemble appelé GTR ou Groupe Turboréacteur comprenant une manche d'entrée d'air qui fait partie de la cellule avion et le turboréacteur lui-même qui assure la propulsion de l'avion. Le turboréacteur quant à lui est constitué des éléments fondamentaux suivants :
- une virole d'entrée encore appelée carter d'admission (qui pour les réacteurs à double-flux intègre un FAN à l'origine de la plus grande partie de la poussée) ;
- un compresseur qui permet d'augmenter la pression et la température de l'air aspiré par le réacteur avant l'injection de carburant ;
- une chambre de combustion où l'augmentation brutale de température de l'air (par injection de carburant) va avoir pour conséquence une augmentation très importante de son volume ;
- une turbine dans laquelle une partie de l'énergie des gaz brûlés va se transformer en énergie mécanique pour entraîner le compresseur et tous les éléments mécaniques rotatifs du réacteur ;
- un canal d'éjection terminé par une tuyère qui assure la mise en vitesse des gaz éjectés.
En plus de ces éléments que l'on retrouve sur tous les types de turboréacteurs on trouve aussi :
- un système de démarrage et d'allumage ;
- un système de régulation ;
- une chaîne cinématique d'entrainement des pompes, alternateurs, etc.
L'aérothermodynamique globale de la veine constituée par tous ces éléments mis bout à bout et qui décrit les transformations successives que subit l'air traversant le turboréacteur nous montre qu'une dégradation du débit d'air au cours de son passage dans la machine se traduit par une perte de poussée .
Ensemble « entrée d'air »

C'est un conduit destiné à capter l'air et à l'amener dans les meilleurs conditions possibles à l'entrée du compresseur. L'ensemble « entrée d'air » comprend l'entrée d'air moteur proprement dite et la manche d'entrée d'air la charge de l'avionneur[Quoi ?].
Entrée d'air moteur
L'entrée d'air moteur est généralement constituée par un carter en alliage léger, qui a souvent la fonction annexe de supporter des accessoires.
Manche d'entrée d'air
La manche d'entrée d'air qui, dans le cas d'un turboréacteur installé sur avion, permet son alimentation en air, peut être disposée de différentes manières (en pitot, en pod, noyée dans les ailes, etc.). Elle peut être munie d'équipements divers (grille de protection, atténuateur de bruit, dispositif anti-givrage, filtre, etc.). Que le turboréacteur soit installé à l'extérieur ou à l'intérieur de la cellule avion, la manche d'entrée d'air aura le rôle d'assurer son alimentation en air dans tout le domaine de vol, et ce quelles que soient les conditions extérieures.
Contraintes principales
Certains critères de qualité sont pris en compte pour la définition de la manche d'entrée d'air, et ce pour tous les types d'appareils équipés de turboréacteurs. Ces critères sont les suivants :
La manche d'entrée d'air :
- doit permettre d'obtenir une pression totale aussi élevée que possible à l'entrée du compresseur, car la poussée brute du turboréacteur en dépend proportionnellement ;
- doit présenter une bonne homogénéité des pressions dans un plan perpendiculaire à l'avancement de l'avion, car des distorsions importantes ont pour conséquence directe une perte de marge au pompage du turboréacteur ;
- doit pouvoir transformer avec un rendement acceptable la vitesse de l'air à l'entrée de la manche (Mach 0,6 en général) en une vitesse satisfaisante pour l'entrée du compresseur (Mach 0,5 en fin de manche) ;
- doit présenter une traînée minimale en fonction de sa géométrie et de sa position sur l'avion.
Fonctionnement au point fixe
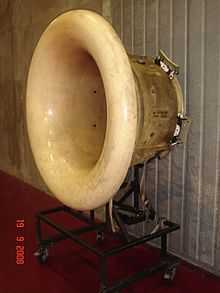
Au point fixe au sol et au roulage, les filets d'air se présentent avec des incidences très importantes à l'entrée de la manche d'entrée d'air, provoquant des décollements et des remous réduisant sa section efficace. Dans les bancs d'essai réacteur ouverts ou fermés, c'est la même raison qui impose d'utiliser une manche d'entrée d'air particulière, appelée pavillon.
Pour les avions (militaires principalement) ayant des entrées d'air à bord mince, l'ouverture de trappes permet à régime élevé et faible vitesse avion une admission d'air supplémentaire permettant de rétablir un débit d'air correct pour le turboréacteur. Pour les avions civils, le profil aérodynamique de l'entrée d'air étant plus épais, le phénomène de décollement est évité. Les avions militaires réduisent également en grande partie les problèmes de fortes incidences au décollage en employant fréquemment des entrées d'air à géométrie variable, qui se trouvent toujours exactement dans le vent relatif (le F-15 en est un bon exemple).
Fonctionnement en vol
La manche d'entrée recevant une énergie de vitesse variable en fonction des conditions de vol devra tantôt ralentir, tantôt accélérer l'air dans l'entrée compresseur.
Vol subsonique
Pour ce domaine de vitesses inférieures au Mach, la manche d'entrée sera un simple divergent, c'est-à-dire qu'elle aura pour effet de diminuer la vitesse en augmentant la pression de l'air à l'entrée compresseur dès que les vitesses en jeu seront supérieures à Mach 0,5. Pour les avions dont c'est le domaine de vol en croisière, l'ensemble moteur et capotage (lorsqu'ils sont installés sous l'aile) ont une position avancée par rapport au bord d'attaque afin d'éviter les perturbations aérodynamiques lors des phases de vol à grande incidence.
Vol supersonique
Dans ce domaine de vol, la vitesse de l'air entrant dans la manche d'entrée devient plus grande que la vitesse du son, ce qui crée une discontinuité dans l'écoulement. Cette discontinuité se traduit par une brutale variation de pression, appelée onde de choc. Si un écoulement d'air pénètre directement dans la manche d'entrée, il y a formation d'une onde de choc droite (perpendiculaire au plan d'entrée), alors que si nous plaçons un obstacle pointu dans cette manche d'entrée, nous aurons formation d'un front d'onde oblique.
La transformation que subit le gaz au passage de l'onde de choc implique une dégradation d'énergie qui se traduit par :
- une diminution de la vitesse d'écoulement ;
- une augmentation de la température ;
- une augmentation de la pression.
La dégradation d'énergie est plus faible dans une onde de choc oblique que dans une onde de choc droite. En aval d'une onde de choc droite, l'écoulement est toujours subsonique. En aval d'une onde oblique, la perte de vitesse étant moins forte, on peut être amené à créer plusieurs zones de chocs pour atteindre des vitesses inférieures au Mach.
Le tableau ci-dessous est donné à titre indicatif pour montrer la réalité de la dégradation d'énergie de part et d'autre d'une onde de choc droite.
M1 Mach en amont |
P2 ----- P1 |
T2 ----- T1 |
M2 Mach en aval |
Diminution de vitesse au travers de l'onde de choc |
---|---|---|---|---|
1,1 | 1,250 | 1,065 | 0,91 | 52 m/s |
2 | 4,50 | 1,690 | 0,577 | 436 m/s |
3 | 10,03 | 2,680 | 0,475 | 755 m/s |
La structure de la manche d'entrée doit présenter des zones de convergence et de divergence, afin de ralentir le flux d'air qui gave le compresseur, tout en récupérant le maximum de pression. Mais cette structure doit être à géométrie variable, c'est-à-dire présenter un canal divergent ou convergent-divergent suivant le domaine de vol, afin d'adapter le débit d'air à toutes les conditions de vol et d'assurer la stabilité des ondes de choc qui assurent le passage de l'écoulement supersonique à un écoulement Subsonique.
Par exemple sur le Mirage 2000, une souris mobile permet :
- de créer une recompression de l'écoulement avant l'entrée d'air divergente située devant le compresseur (au travers d'ondes de choc obliques) ;
- de dévier plus ou moins d'air excédentaire à l'extérieur, pour s'adapter aux différents rapports débit/vitesse de vol (gavage efficace du moteur).
L'adaptation de la manche aux grands angles d'attaque est réalisée grâce à des trappes et des pelles se trouvant sur les flancs inférieurs de la manche. La Manche d'entrée d'air du Mirage 2000 comprend :
- deux corps centraux bicoques, appelés « souris » ;
- deux pièges à couche limite ;
- quatre entrées d'air additionnelles ;
- deux pelles ;
- un divergent.
L'adaptation de la manche d'entrée d'air du Mirage 2000 est réalisée par les souris mobiles qui :
- permettent à l'écoulement d'être toujours de nature critique, c'est-à-dire de permettre un positionnement des ondes de choc tel que la traînée qui en résulte soit minimisée ;
- ajustent la section d'entrée en fonction du débit d'air requis pour le bon fonctionnement du turboréacteur.
Compresseur
Rôle du compresseur
Le mélange air kérosène ne pouvant s'enflammer que dans certaines conditions de pression et de température, les motoristes ont intégré un compresseur avant la chambre de combustion. Le compresseur a pour fonction d'élever la pression, ainsi que la température, du fluide entre l'entrée et la sortie par transformation de l'énergie cinétique :
- en énergie de pression par effet centrifuge dans un compresseur centrifuge ;
- en énergie de pression par diminution de volume et ralentissement du fluide dans les grilles fixes et mobiles d'un compresseur axial.
La poussée du turboréacteur dépend essentiellement du débit d'air entrant et de la vitesse d'éjection à la sortie de la tuyère, elle-même dépendant de la température des gaz en fin de combustion. Pour améliorer le rendement tout en diminuant la consommation de carburant et en chauffant à la limite de la métallurgie, il a fallu augmenter le taux de compression à l'entrée de la chambre de combustion tout en assurant la combustion continue du carburant injecté. Cela a nécessité l'utilisation d'un compresseur dont la réalisation a suivi deux principes très différents :
- la compression par effet centrifuge se traduisant par une augmentation de la vitesse (énergie cinétique) des gaz et dont la technique est quasiment abandonnée au début du XXIe siècle ;
- la compression par ralentissement du fluide et diminution du volume des gaz dans l'axe de rotation du moteur — le compresseur axial — actuellement généralisée sur tous les types de turboréacteurs.
Compresseur centrifuge

Généralités
Les premiers turboréacteurs, conçus à partir des prototypes mis au point par Whittle et Von Ohain, sont munis d'un compresseur centrifuge qui est entraîné par la turbine. Ils ont le mérite de la simplicité, étant donné qu'un seul étage d'aubes réalise la compression et qu'un seul arbre relie la turbine au compresseur[22].
Leur faible longueur s'accompagne d'un fort diamètre nécessaire à une bonne compression. L'air atteint en effet sa compression maximale à l'extrémité du compresseur puisque la force centrifuge est d'autant plus grande que son point d'application est éloigné de l'axe de rotation[22]. Ce fort diamètre le destine plutôt à des turboréacteurs de faible dimension.
Les premiers réacteurs anglais tels que les Goblin des De Havilland Vampire ou les Rolls-Royce Welland du Gloster Meteor sont ainsi conçus[23]. Par ailleurs, la plupart des turbines pour hélicoptères restent conçues sur ce principe qui permet la conception de moteurs compacts.
Constitution
Le compresseur centrifuge se compose essentiellement d'un Rotor (ou roue centrifuge) à ailettes radiales et d'un ou plusieurs diffuseurs. Dans le rotor, l'air pénètre axialement et s'écoule ensuite radialement. La vitesse de l'air augmente du fait de l'accélération centrifuge et sa pression du fait de la section divergente entre les aubes. L'air quitte l'extrémité des pales du rotor à très grande vitesse et dans le stator une partie de cette vitesse est transformée en pression du fait de la section divergente des aubes.
Performances
Le compresseur centrifuge est simple, robuste et de bon rendement, mais son taux de compression est limité à une valeur relativement faible ce qui le condamne à une utilisation dans les turbomachines de faible puissance. À la fin des années 1940, le taux de compression maximum est d'environ 4[24].
Compresseur axial

L'augmentation croissante du poids des aéronefs amène les ingénieurs en aéronautique à imaginer des solutions pour améliorer la poussée fournie par le turboréacteur[25]. Du fait de la moindre efficacité, ils nécessitent plusieurs étages tournant à la même vitesse mais peuvent supporter des vitesses de rotation nettement plus élevées. Le premier de ce type, et aussi le premier construit en grande série, est le Jumo 004 de Junkers-Motoren qui équipait le Messerschmitt Me 262[6].
Les progrès de la métallurgie permettent de réaliser des compresseurs axiaux constitués pour chaque étage d'une roue mobile et d'une grille fixe permettant de réaliser une phase complète de compression. Plus le nombre d'étages est grand, plus le taux de compression est élevé.
Caractéristiques principales
Le tableau ci-dessous est donné à titre indicatif pour montrer différentes caractéristiques de compresseurs axiaux :
Moteurs | Pression sortie -------------------- Pression entrée |
Température sortie | Caractéristiques technologiques |
---|---|---|---|
ATAR | 6,11 | 250 °C | Simple corps, 9 étages |
LARZAC | 10,8 | 370 °C | Double-corps, BP 2 étages + HP 4 étages |
M53 au sol | 8,5 | 325 °C | Simple corps, 3 + 5 étages |
M53 à Mach 2,3 | 8,5 | 430 °C | Simple corps, 3 + 5 étages |
CFM56-2 | 24 | 550 °C | Double-corps, 1 soufflante, BP 3 étages + HP 9 étages |
Technologie
Le compresseur est constitué :
- d'une partie tournante - le rotor ;
- d'une partie fixe - le stator ;
- d'une enveloppe - le carter.
- Le rotor comprend un tambour constitué par l'assemblage de plusieurs disques sur lesquels sont fixées les aubes et un ensemble d'aubes montées sur un disque s'appelle une roue mobile
- Le stator est constitué de plusieurs rangées d'aubes fixées sur le carter (cas de l'ATAR - SNECMA) ou sur des viroles (cas du M53 - SNECMA); chaque rangée d'aubes fixes s'appelle grille fixe ou redresseur.
Les aubes ont un profil aérodynamique avec un bord d'attaque arrondi (tolérant les variations d'incidence) et un bord de fuite aminci (pour diminuer le sillage). Elles présentent un angle de calage par rapport à la génératrice du rotor, ce qui impose le sens de l'écoulement. Elles sont également vrillées afin que les filets d'air présentent un angle d'incidence constant entre la tête de l'aube et son pied qui n'ont pas la même vitesse circonférentielle.
L'air traverse alternativement une roue mobile puis une grille fixe (soit un étage compresseur) qui réalise une phase complète de compression. Pour augmenter le taux de compression du moteur, il suffit d'augmenter le nombre d'étages. La compression s'accompagnant d'une diminution du volume, la veine est de forme convergente de l'entrée vers la sortie du compresseur afin de maintenir les rapports de pression entre chaque étage.
Principe de fonctionnement
Le principe élémentaire de compression d'un étage compresseur est le suivant :
- mise en vitesse de l'air par effet dynamique dans la roue mobile et légère augmentation de sa pression statique par ralentissement lors du passage dans le divergent créé entre deux aubes consécutives ;
- redressement de l'air après passage dans la roue mobile et augmentation de sa pression par ralentissement dans le divergent créé par deux aubes fixes consécutives ;
- augmentation de la température de l'air à la suite de sa compression.
En augmentant le nombre d'étages (rotor + stator), on augmente le taux de compression global et la température à la sortie du compresseur.
En résumé, dans un étage de compresseur, qui comprend une grille mobile et une grille fixe :
- La grille mobile apporte l'énergie en augmentant la vitesse relative de l'écoulement ;
- La grille fixe ramène l'écoulement dans l'axe et augmente la pression en diminuant la vitesse absolue de l'écoulement.
Dans un compresseur axial, la vitesse de déplacement axiale du flux est à peu près constante en grandeur et direction : la valeur de cette vitesse est généralement comprise entre 130 m/s et 170 m/s.
Limites de fonctionnement
Des limites de fonctionnement apparaissent :
- le pompage ;
- le décrochage ;
- la vitesse de rotation ;
- le niveau vibratoire ;
- la température ;
- Le pompage se traduit par des oscillations brutales de la pression et du débit de l'air traversant le turboréacteur. Il est souvent causé par le décollement de l'écoulement sur l'aube.
- Le décrochage est lié à une diminution brutale du débit à vitesse constante il a pour conséquence de rendre la pression dans la chambre de combustion supérieure à la pression de refoulement du compresseur et de conduire à l'extinction de la chambre de combustion par une inversion de l'écoulement.
- Les aubes sont soumises à la force centrifuge qui est proportionnelle au carré de la vitesse de rotation. Malgré un dimensionnement adapté aux plus sévères contraintes, cette vitesse est une limite à ne pas dépasser sous peine de rupture.
- L'aube, en forme de lame, peut vibrer à une fréquence propre qui dépend de ses dimensions, de sa forme et de son mode de fixation. Un certain nombre de phénomènes peuvent exciter et entretenir des vibrations mécaniques pouvant amener à la rupture, tels que :
- les sillages de bord de fuite ;
- les balourds dus à des défauts d'équilibrage ;
- des instabilités aérodynamiques (liées aux décollements des filets d'air).
- Le nombre de Mach maximal d'un turboréacteur est lié principalement à l'élévation de température qui traverse le compresseur, qui elle-même dépend :
- de la vitesse de vol ;
- du rapport de pressions du compresseur.
Champ compresseur

La qualité de la transformation en énergie de pression est caractérisée par le rendement de compression ηc =P2/P1, les pertes dans un étage pouvant être :
- aérodynamique ;
- par écoulement ;
- mécaniques.
Dans le champ de fonctionnement du compresseur (Taux de compression;Débit), il existe une ligne unique sur laquelle se placent tous les points de fonctionnement possibles pour un compresseur donné : c'est la ligne de fonctionnement (ou ligne de travail) qui fait correspondre un débit et un taux de compression pour un régime de rotation donné (lignes d'iso-vitesses).
Cette ligne de fonctionnement est indépendante des conditions extérieures (pression, température) ainsi que des conditions de vol du moteur (nombre de Mach, altitude). Cette ligne de fonctionnement coupant les iso-vitesses du champ de fonctionnement elle peut être traduite en vitesse de rotation du compresseur. En clair, si on connait la vitesse du compresseur, on sait si le point de fonctionnement pour cette vitesse de rotation est sur la ligne de fonctionnement stable du compresseur, c'est-à-dire si cela correspond au débit et au taux de compression correcte.
Une autre ligne de fonctionnement dite « ligne de pompage » est constituée des points de fonctionnement compresseur ou le rendement chute à la suite du décrochage aérodynamique des aubes. La distance entre ces deux lignes de fonctionnement est appelée « marge au pompage ».
Si l'air entre deux aubes consécutives atteint la vitesse du son le débit d'air se bloque sur le front de pression engendré.
À vitesse élevée, le pompage est lié au décollement des derniers étages et au blocage des étages de tête alors qu'à basse vitesse c'est le contraire.
Le décrochage du compresseur ne lui permet plus d'assurer le niveau de pression en aval de la chambre de combustion. Les conséquences sont alors catastrophiques sur le fonctionnement du moteur du point de vue de la performance et de la sécurité (risque de détérioration mécanique, d'extinction du moteur).
Solutions multi-corps


Dans chaque étage, on a une augmentation de pression mais aussi de température; or, pour un étage donné, le rapport de pression entrée-sortie est d'autant plus élevé que la température d'entrée est faible (l'air moins dilaté se comprime plus facilement). Pour une vitesse de rotation donnée de tous les étages, les températures d'entrée dans chaque étage augmentent au fur et à mesure de la progression du flux et donc le taux de compression par étage diminue (car pour un étage donné le taux de compression est d'autant plus élevé que la température d'entrée dans l'étage est basse).
Dans un compresseur axial, les rapports de pression de chacun des étages vont donc en décroissant et pour conserver des rapports de pression élevés par étage, il faudrait augmenter la vitesse de rotation des étages les plus chauds, d'où l'idée d'avoir plusieurs compresseurs tournant à des vitesses différentes et la réalisation de solutions multicorps (double corps, triple corps).
Par exemple les avantages du double corps par rapport à un simple corps sont :
- moins de pompage aux bas régimes (le corps HP tourne plus vite ce qui évite le bourrage) ;
- le rendement de compression est amélioré aux bas régimes ;
- la poussée au ralenti est plus faible et la consommation est diminuée ;
- le démarrage est facilité car seul le corps HP est lancé ;
- les accélérations sont plus rapides par une inertie diminuée.
Les multi corps sont plus complexes et leur coût initial est plus élevé mais en exploitation la différence est en faveur du multi corps.
Chambre de combustion
Généralités
La chambre de combustion est la partie du turboréacteur qui a pour rôle d'élever la température de l'air issu du compresseur par combustion de carburant afin de fournir des gaz chauds à la turbine et de participer à la propulsion à travers leur détente dans la tuyère d'éjection.
La combustion doit y être optimale et l'écoulement dans la partie aval du turboréacteur ne doit pas subir de perte de charge [perte de pression] trop importante. L'air doit traverser la chambre à vitesse relativement faible, moins de 100 m/s. La flamme est confinée dans une zone à très basse vitesse alimentée par environ le dixième du débit d'air qui traverse la chambre et la température au point le plus élevé approche les 2 000 °C. La température s'abaisse très rapidement par dilution avec le reste de l'air traversant la chambre afin d'atteindre une valeur compatible avec la tenue des matériaux de la turbine. Pour assurer une bonne tenue mécanique des parois de la chambre il faut limiter la température aux alentours de 900 °C (dépend des matériaux réfractaires employés).
Réaction de combustion
Le mécanisme de combustion des hydrocarbures dans l'air est une réaction exothermique qui implique que le mélange carburé :
- soit à l'état gazeux et dans un rapport de richesse optimal dit stœchiométrique ;
- soit à une température minimum qui permette l'allumage ;
- soit à une pression minimum.
La température de flamme atteint alors un maximum pour ces conditions et augmente avec la température initiale du mélange. Cette température chute rapidement si ces conditions ne sont pas réunies.
La température d'allumage permettant une réaction chimique avec flamme permet :
- l'inflammation spontanée du mélange si celle-ci est maintenue ;
- l'inflammation assistée si un point du mélange est porté au-dessus de celle-ci.
L'énergie nécessaire à fournir pour l'allumage est d'autant plus importante que :
- la température du mélange est basse et la volatilité du carburant est faible ;
- la pression du mélange est faible ;
- la richesse du mélange est différente du rapport stœchiométrique ;
- la vitesse d'écoulement du mélange est grande.
Les limites de combustion autonome sont :
- la richesse du mélange par excès de carburant ;
- la pauvreté du mélange par défaut de carburant ;
- la richesse gazeuse maximale qui limite la combustion dans les basses températures du mélange ;
- la zone d'auto-allumage qui limite le fonctionnement dans les hautes températures du mélange.
Dans un écoulement laminaire le front de flamme suit la variation de vitesse d'écoulement du mélange mais dans la chambre de combustion d'un turboréacteur l'écoulement du mélange est fortement turbulent. Le brassage des produits de combustion avec le mélange arrivant dans la chambre conduit à une combustion généralisée dans l'enceinte avec des temps de réaction très courts. Si le débit augmente trop, le temps de maintien du mélange frais dans la chambre deviendra inférieur au délai d'allumage et la flamme sera expulsée de l'enceinte de combustion : c'est le phénomène de soufflage encore appelé « blow out ».
Les causes d'extinction d'une chambre de combustion sont multiples mais tiennent à deux phénomènes principaux :
- une vitesse de réaction trop faible due principalement à une pression du mélange trop faible et (ou) une température de flamme trop basse
- un temps de maintien insuffisant du mélange carburé causé principalement par une vaporisation trop lente du carburant et (ou) une vitesse d'écoulement du mélange carburé trop grande
Évidemment l'extinction en vol peut constituer, si elle est multiple, un risque d'accident car la probabilité d'un ré-allumage en vol dépend :
- du temps disponible avant l'arrivée au sol (ex. : sans motorisation à une altitude de 10 000 ft pour une vitesse de 250 kts, un A320 (masse 60 t) descend à 1 800 ft/min) ;
- du stress de l'équipage dans ce genre de situation ;
- des conditions dégradées des facteurs de ré-allumage (perte de pression de gavage, allumage sur une seule bougie, régime d'autorisation faible, météo).
Performances d'une chambre de combustion
Rendement
Si Q est la quantité de chaleur libérée chaque seconde par la combustion du carburant et Q' la quantité de chaleur que l'on pourrait obtenir par une combustion complète, le rapport ? = Q/Q' représente le rendement de la chambre de combustion. La consommation spécifique est liée au rendement de combustion. Pour l'améliorer, il faut assurer un mélange comburant-carburant aussi intime que possible par obtention d'un écoulement tourbillonnaire entre les écoulements linéaires à l'entrée et à la sortie. La conception aérodynamique de la chambre de combustion est donc particulièrement compliquée.
Paramètres influençant la combustion
Les principaux paramètres influençant la combustion sont :
- la température d'entrée dans la chambre ;
- la pression d'entrée dans la chambre ;
- la vitesse d'écoulement à l'entrée de la chambre.
La richesse dépend des températures d'entrée et de sortie de la chambre mais aussi des conditions de vol. Elle est maximale au décollage, elle diminue en croisière et peut atteindre en régime transitoire (par exemple sur une réduction brutale des gaz) une valeur minimale. La richesse peut varier dans un rapport de 1 à 10 suivant les moteurs et les conditions d'utilisation en vol.
La pression à l'entrée de la chambre peut varier de 0,2 bar à 30 bar et la température d'entrée de −40 °C à 650 °C suivant le domaine de fonctionnement du turboréacteur.
D'autre part, pour certaines conditions de vol la chambre doit pouvoir se rallumer et avoir une plage de fonctionnement stable pour l'autorotation (avion militaire) après extinction en altitude. Après réallumage, la combustion doit permettre une accélération du moteur à des altitudes supérieures à 10 000 m, suivant le type d'avion.
Carburants aéronautiques
Propriétés générales
Un carburant aéronautique doit avoir les caractéristiques suivantes :
- un fort pouvoir calorifique par unité de masse pour favoriser l'autonomie de vol ;
- une forte masse volumique pour diminuer le volume des réservoirs à masse donnée ;
- une faible inflammabilité aux conditions de température et de pression d'emploi, pour augmenter la sécurité du vol ;
- un bon pouvoir lubrifiant pour garantir une bonne durée de vie des pompes et différents organes traversés par le carburant ;
- un prix compatible avec l'économie du transport aérien pour le civil.
Aujourd'hui c'est un hydrocarbure insaturé, le kérosène, qui répond le mieux à tous ces critères.
Caractéristiques des différents carburants utilisés en aéronautique
- Densité : 0,8 pour TRO (F34,F35) et 0,75 pour TR4 (F40)
- Pouvoir calorifique inférieur : 43 054 J/kg
- Richesse stœchiométrique : Dc/Da = 0,06
- Température maximale après combustion : environ 2 200 K avec de l'air à 300 K
- ɣ=Cp/Cv des gaz brûlés à 1 000 K : 1,3
- ɣ=Cp/Cv des gaz brûlés à 2 000 K : 1,2
Nota : le kérosène et l'oxygène pur donnent une température de 3 500 K lorsque le mélange est stœchiométrique.
Vitesse de flamme - stabilité de combustion
La vitesse du front de flamme (dans un mélange homogène) est relativement faible par rapport à la vitesse d'écoulement du fluide dans un turboréacteur et augmente :
- avec la pression du mélange ;
- avec la densité des gouttelettes de carburant et leur pression d'injection dans la chambre.
Pour que la combustion soit possible, il faut que la vitesse de l'écoulement ne soit pas supérieure à la vitesse de propagation de la flamme. Donc pour qu'une injection en continu du carburant puisse donner une flamme stable il faut que les gouttelettes de carburant injectées rencontrent rapidement les gouttelettes de carburant allumées afin de récupérer assez d'énergie pour leur propre allumage.
Afin d'éviter un soufflage de la flamme l'écoulement est ralenti à des vitesses compatibles avec la combustion. Pour ce faire la chambre est raccordée au compresseur situé en amont par un divergent.
Turbine

But
La turbine a pour fonction de transformer l'énergie de pression des gaz en sortie de la chambre de combustion en énergie cinétique, puis en énergie mécanique afin d'entrainer le FAN ou soufflante, le compresseur et les différents équipements de servitude. L'énergie restante à la sortie de la turbine participe à la poussée du réacteur.
Principe
Dans un écoulement subsonique, la relation entre la vitesse, la pression et la masse volumique du fluide est caractérisée par le théorème de Bernoulli. La détente des gaz dans la turbine est obtenue par l'accélération du fluide dans un convergent et une partie de l'énergie cinétique récupérée est transformée en travail moteur.
Descriptif et fonctionnement
En général les turbines rencontrées sur turboréacteur sont de type axiale ; l'écoulement est donc parallèle à l'axe du moteur. L'étage de détente d'une turbine se compose d'une grille d'aubes fixes appelée [Distributeur] et d'une grille d'aubes mobiles appelée [Roue]. Lorsque la puissance à prélever dépasse les possibilités d'un seul étage, on utilise des turbines à plusieurs étages.
Rôle du distributeur
Les gaz à la sortie de la chambre de combustion pénètrent dans le distributeur qui les dévie d'un angle dans la direction tangentielle de la [Roue]. Il transforme leur énergie de pression en énergie cinétique par effet convergent. L'accélération de l'écoulement ainsi obtenue s'accompagne d'une diminution de pression et de température.
Rôle de la Roue
Les gaz à la sortie du distributeur pénètrent dans la [Roue] mobile avec un angle d'incidence qui entraîne une distribution inégale des pressions sur l'intrados et l'extrados des aubes. La pression exercée par le fluide sur l'intrados est supérieure à celle exercée sur l'extrados et cela crée une résultante aérodynamique qui met la [Roue] mobile en mouvement réalisant la transformation d'une partie de l'énergie cinétique en énergie mécanique.
Pour augmenter l'énergie mécanique utile il faut :
- soit augmenter la vitesse du fluide ;
- soit augmenter l'angle d'incidence
;
- soit agir sur les deux à la fois.
Performances
Puissance développée
La puissance développée par une turbine peut s'exprimer par la formule suivante :
![W=J*(D5+dc)*[(Cp5*T5)-(Cp6*T6)]](../i/m/925a255b27ae650140451ba4b771f5c9.png)
avec
Calcul de la puissance développée par le moteur Olympus au sol avec les valeurs suivantes des paramètres :
- D5 = 182,4 kg·s-1 ;
- dc = 3,4 kg·s-1 ;
- T5 = 1 293 K ;
- T6 = 948 K ;
pour = 0,01865 valeur de la richesse du mélange air-carburant nous avons les valeurs suivantes de chaleur spécifique :
- pour T5 = 1 293 K
Cp5 = 0,2626
- pour T6 = 948 K
Cp6 = 0,2537
la puissance développée par la turbine du moteur Olympus est alors W = 77 600 000 W ou 105 300 ch
cette puissance qui est une petite partie de la puissance globale du réacteur sert essentiellement à entraîner le compresseur et les équipements.
Limitations
La turbine est l'organe du turboréacteur qui travaille dans les conditions les plus sévères :
- haute température ;
- efforts centrifuges importants ;
- contraintes thermiques élevées, notamment lors des allumages et des extinctions de la chambre de combustion ;
- atmosphère oxydante ;
- vibrations lors des passages dans les régimes de résonance.
De plus toute augmentation de la vitesse des gaz entraîne une augmentation de la vitesse de rotation de la roue mobile et donc de la vitesse circonférentielle, limitée par des considérations de résistance mécanique. Une augmentation trop importante de l'angle d'incidence du flux par rapport au calage des aubes conduirait à des perturbations aérodynamiques entrainant des pertes de charge trop importantes.
Pendant une compression adiabatique il y a augmentation de l'enthalpie et pour une détente c'est l'inverse qui se produit cela a pour conséquence qu'une turbine peut absorber plus d'énergie qu'un étage de compresseur peut en fournir. C'est pour cette raison aussi que le phénomène de pompage ou de décollement tournant est inexistant dans une turbine.
L'accroissement de la puissance absorbée par la turbine est obtenu grâce à l'ouverture de la section de tuyère (ou du col du distributeur aval) pour augmenter la détente. La qualité d'une turbine est évaluée par son rendement de détente et sa limite de puissance absorbée dépend de la vitesse de l'air entre ses aubes (blocage si Mach=1).
Rendement
Comme dans la manche d'entrée, le compresseur ou la chambre de combustion, la transformation que subit l'écoulement dans la turbine est imparfaite, d'où la notion de rendement :
- P5 pression réelle entrée turbine ;
- P6 pression réelle sortie turbine ;
- T5 température réelle entrée turbine ;
- T6 température réelle de sortie turbine ;
- T6th température théorique de sortie turbine ;
- Sr section de sortie du rotor.
Si la transformation d'énergie était sans pertes on aurait :
à partir de cette équation et connaissant P5, P6 et T5 on peut calculer la T6th qui est toujours supérieure à la T6 réelle et de ce fait le rendement réel de la turbine est approximativement :
Refroidissement des aubes
Rôle
L'obligation de réduire la consommation en carburant nécessite d'avoir des températures plus élevées à l'entrée de la Turbine et d'augmenter le taux de compression en aval car le gain en SFC est d'autant plus grand que celui-ci est plus élevé.
L'augmentation de la température à l'entrée de la Turbine permet également :
- d'augmenter la poussée par unité de débit d'air chauffé ;
- de réduire la masse de carburant à emporter ou d'augmenter le rayon d'action ;
- et pour une poussée donnée de réduire les dimensions et le poids du moteur.
Principe
Le refroidissement des aubes est réalisé par convection en utilisant de l'air plus frais prélevé sur le compresseur aval. Ce prélèvement fait au détriment des performances se pose au motoriste en termes de compromis et de bilan.
Le refroidissement des aubes autorise des températures plus élevées, ce qui améliore le rendement global du cycle de la Turbine mais cela correspond à un déficit au niveau du moteur car il a fallu dépenser plus d'énergie pour le comprimer alors qu'il n'intervient pas dans la poussée.
Actuellement avec les températures atteintes en sortie de chambre de combustion et au vu des débits de refroidissement adoptés, le bilan global est positif.
Deux procédés principaux sont utilisés pour assurer la refroidissement des aubes de turbine :
- la convection interne ;
- le film protecteur.
Convection interne
Le refroidissement de la paroi extérieure de l'aube est assuré par échange de calories entre les gaz chauds extérieurs et les gaz frais circulant à l'intérieur de l'aubage et rejetés au bord de fuite. Les aubes qui sont creuses sont équipées de conduits de type :
- chemisage pour les aubes fixes (distributeurs) ;
- canaux ou cavités pour les aubes mobiles.
Film protecteur
Le refroidissement par convection interne peut être complété par un refroidissement des parois par film protecteur. On prélève sur le débit d'air frais qui circule dans l'aube un débit d'air qui est projeté à l'extérieur sur les bords d'attaque et de fuite pour créer une paroi fluide protectrice qui isole l'extérieur de l'aube des gaz chauds.
Le film d'air protecteur est créé au moyen de petits trous percés au bord d'attaque ou au bord de fuite par laser ou électro-érosion.
Technologie
La métallurgie des aubes a évoluée depuis la fabrication des aubes par coulage en passant par les alliages à solidification dirigée pour aboutir aux aubes monocristallines pour lesquelles les gains en températures sont très importants. La métallurgie des disques de Turbine a aussi évoluée dans le sens d'une meilleure tenue mécanique et thermique avec l'augmentation des vitesses de rotation et des températures de sortie de chambre de combustion.
Fabrication des aubes
Une autre façon d'améliorer la tenue en température des aubes de turbine est d'élaborer de nouveaux matériaux résistants à très haute température et de faire évoluer la métallurgie des alliages utilisés dans leur fabrication.
Alliages
Un alliage est constitué d'un ou plusieurs métaux de base appelés matrice auxquels on ajoute des éléments chimiques permettant d'améliorer certaines propriétés de celui-ci telles que :
- résistance mécanique ;
- dureté ;
- résistance à la corrosion ;
- tenue au fluage ;
- etc.
À l'échelle microscopique, un alliage apparaît comme un agglomérat de grains (cristaux). Si la solidification est réalisée sans précaution particulière, l'orientation des grains est désordonnée et les caractéristiques du matériau sont sensiblement les mêmes dans toutes les directions : on parle alors d'une structure EQUIAXE.
Afin de privilégier un axe de travail permettant une meilleure tenue mécanique, il existe des procédés qui permettent de diriger les cristaux dans un sens privilégié : on parle alors d'alliage à solidification dirigée.
D'autres procédés permettent d'obtenir des alliages avec un seul grain, ce qui leur confère des propriétés encore meilleures le problème résidant essentiellement dans l'obtention de pièces monocristallines de dimensions importantes.
Certains alliage dits "Eutectiques" se solidifient à température constante comme les corps pur et permettent d'obtenir des structures à grains fins et homogènes.
Un autre procédé appelé " Métallurgie des Poudres" permet en mélangeant les composants sous forme pulvérulente puis en les compactant sous forte pression d'obtenir des pièces directement à leur cotes finies tels que les disques de turbine.
Typologie
Dans les turboréacteurs double-corps, la turbine est constituée d'un ou plusieurs étages (stator-rotor) à haute pression (HP) et d'un second à basse pression. La turbine HP, dont les ailettes sont soumises au flux des gaz de combustion les plus chauds, est la pièce la plus compliquée sur les plans de la tenue des matériaux et de l'aérodynamique. Il existe deux types de turbine, l'une à action et l'autre à réaction.
Dans une turbine à action (solution privilégiée pour les turbopropulseurs et les turbomoteurs), le travail de détente (quasi complet) ne s'effectue que dans le stator. L'énergie cinétique ainsi engendrée sera récupérée sous forme d'énergie mécanique afin d'entraîner le compresseur, le réducteur, l'hélice ou la voilure tournante suivant le cas, ainsi que les accessoires nécessaires au moteur.
Dans une turbine à réaction, la détente s'effectue à la fois dans le stator et dans le rotor. De plus, dans ce type de turbine, seule une "faible" partie de l'énergie des gaz est détendue afin de la récupérer sous forme d'énergie mécanique, étant donné que l'ensemble turbine-compresseur (ajouter à cela la soufflante) est moins "lourd" à entraîner qu'un ensemble avec hélice. Le restant d'énergie sera récupéré au niveau de la tuyère, sous forme d'énergie cinétique, afin de créer la poussée.
Canal d'éjection
Généralités
C'est dans le canal d'éjection qu'a lieu la détente utile à la propulsion par transformation en vitesse de l'énergie restante (pression et température) des gaz après passage dans la turbine. La poussée du turboréacteur sera d'autant plus forte que la vitesse d'éjection sera plus grande.
Le canal d'éjection est constitué, pour les moteur sans postcombustion, d'un carter d'échappement et d'une tuyère. Pour les moteurs avec postcombustion, le canal d'éjection comprend un système de réchauffe situé entre le carter d'échappement et la tuyère d'éjection.
Carter d'échappement
Le carter d'échappement situé derrière la turbine assure la continuité intérieure et extérieure de la veine permettant de séparer, sur les moteurs à double-flux, le flux chaud du flux froid.
Tuyère d'éjection
Rôle d'une tuyère d'éjection
À l'intérieur du turboréacteur l'écoulement du flux est subsonique et si on prolonge la sortie de la turbine par une tuyère cela permet d'accélérer la masse de gaz jusqu'à la section de sortie appelée Col, convergente pour les plus simples, section qui détermine le débit maximal de gaz pouvant être éjecté. La tuyère assure donc l'éjection des gaz brûles et leur retour à la pression ambiante pour que l'accélération du flux qui en résulte génère la poussée du turboréacteur.
Fonctionnement
La section d'éjection de la tuyère est déterminée en pratique pour que, au régime maximum du moteur, la vitesse de l'écoulement y atteigne la vitesse du son, soit Mach 1, et que la pression statique au Col soit égale à la Pression Atmosphérique.
Si la vitesse de l'écoulement est inférieure à la vitesse du son, le débit masse éjecté n'est pas maximum, les gaz se détendent à la Pression Atmosphérique au col et la tuyère est dite adaptée : ce cas correspond à tous les régimes inférieurs au régime maximal.
Le fonctionnement optimal de la tuyère étant obtenu pour une tuyère adaptée (pression au col = Pression Atmosphérique) il a été développé le principe de tuyère à section variable permettant d'adapter la section de sortie au différents régimes du moteur.
Pour les moteurs sans réchauffe, la tuyère convergente-divergente permet, l'écoulement au col étant sonique, d'accélérer le flux dans le divergent pour obtenir une poussée supplémentaire, la vitesse d'éjection des gaz pouvant être alors supersonique.
Le régime d'utilisation des moteurs étant variable suivant le domaine de vol, la partie divergente doit être variable sinon en cas d'écoulement subsonique au col le divergent ralentirait le flux et le rendement de la tuyère chuterait.
Quand la pression statique des gaz est trop forte (supérieure à deux fois la pression atmosphérique) le simple tronc de cône conduit à un éclatement du jet ; on observe alors une série d'ondes de choc jusqu'à ce que la pression statique du jet soit égale à la Pression Atmosphérique. Ces chocs qui se traduisent par une perte d'énergie inutilisable dans la propulsion font chuter le rendement global de la tuyère.
Caractéristiques
La tuyère se situe en aval de la turbine et est composée pour la plus simple d'un tronc de cône dont la section amont est supérieure à la section aval. Pour éviter l'éclatement du jet et la création d'ondes de choc on utilise des tuyères convergente-divergente. Pour les moteurs avec réchauffe on peut utiliser des tuyères à sortie divergente et de section variable.
Certaines tuyères peuvent également recevoir des accessoires tels que :
- un silencieux ;
- un inverseur de poussée.
Rendement propulsif
Dans un turboréacteur l'ensemble compresseur;chambre de combustion;turbine fournit des gaz comprimés et chauds qui libèrent leur énergie dans le but d'assurer la propulsion de l'avion. Il convient de libérer cette énergie avec le maximum d'efficacité en consommant le moins de carburant possible. Il est nécessaire d'optimiser alors le rendement propulsif.
D'une manière générale le rendement propulsif diminue lorsque croît la vitesse d'éjection ce qui nous amène à la conclusion que pour les vitesses subsoniques il faut ralentir la vitesse d'éjection et augmenter la masse de fluide éjectée afin d'obtenir la poussée nécessaire. Cela étant il a fallu trouver des solutions peu gourmandes en carburant et aujourd'hui la technique du double-flux à fort taux de dilution est couramment employée en aviation commerciale.
Le principe général en est le suivant :
- on utilise la température maximale permise par la métallurgie ;
- on augmente le taux de compression pour valoriser au maximum cette température afin de l'obtenir avec moins de carburant (optimisation du rendement thermique) ;
- on fait travailler les gaz chauds dans une turbine avant leur éjection pour mettre en vitesse un débit d'air frais qui participe à la propulsion.
Autrement dit le fluide servant à la propulsion se scinde en deux flux :
- le flux primaire ou flux chaud qui a suivi le processus thermodynamique ;
- le flux secondaire ou flux froid qui ne reçoit que de l'énergie mécanique.
Le rendement propulsif du moteur est augmenté dans des proportions importantes pour des valeurs de dilution voisine de 5 et les vitesses d'éjection sont telles que le flux froid produit 80 % de la poussée totale.
Typologie
Parmi les Turbomachines utilisées dans l'aviation on distingue dans la catégorie des Turboréacteurs plusieurs types :
- Les Turboréacteurs simple-flux appelés ainsi car un seul flux d'air traverse le générateur de gaz
- Les Turboréacteurs double-flux constitués par un générateur de gaz (flux primaire chaud) autour duquel est canalisé un flux secondaire (froid) engendré par une soufflante chargée de capter un débit supérieur à celui du générateur de gaz.
Dans chacun de ces types de machines ont été développées des structures de type :
- Simple-corps
- Multi-corps
De ces deux caractéristiques ont été développées des variantes répondant chacune à des problématiques de caractéristiques de poussée, de rendement, de coût, etc. en fonction des besoins des avionneurs.
Une chronologie dépendante des évolutions techniques et technologiques a fait que les premiers turboréacteurs étaient simple-flux et mono-corps. Ils étaient équipés d'un générateur de gaz comprenant un seul ensemble compresseur-turbine liés, le compresseur pouvant être de type centrifuge ou axial.
Actuellement pour accroître les performances en poussée et consommation de carburant le compresseur a été scindé en plusieurs parties tournant à des vitesses différentes. Afin de permettre l'entrainement de ces compresseurs, des turbines elles-mêmes différentes leur ont été couplées.
Chaque couple compresseur-turbine liée est appelé Corps ou Attelage et aujourd'hui un turboréacteur simple flux ou double flux peut être de type Mono-Corps, Double-Corps ou Triple-Corps suivant les constructeurs et les domaines d'utilisation[26].
Simple corps
![]() |
![]() | |
Le moteur Avia M-04, copie du Junkers Jumo 004 B-1 équipant le Me 262, fonctionne sur le principe du compresseur axial simple corps. |
Dans ce type de machine, le générateur de gaz comprend un seul ensemble tournant appelé Corps et qui comprend un compresseur et une turbine accouplés sur un même arbre et tournant donc à la même vitesse.
Multicorps
La solution double-corps peut s'appliquer au turboréacteur double-flux aussi bien qu'au turboréacteur simple-flux. C'est une technologie complexe qui permet de gagner du poids et de la longueur et qui en outre permet des démarrages nécessitant une plus faible puissance.
Dans ce type de machine, le générateur de gaz comporte deux ensembles tournants mécaniquement indépendants :
- un corps compresseur-turbine dit BP ;
- un corps compresseur-turbine dit HP.
La turbine liée au compresseur BP est appelée turbine BP et celle liée au compresseur HP est appelée turbine HP
Chacun des couples compresseur-turbine tourne à sa vitesse propre et on parle alors de turboréacteurs double corps ou double attelage[25]. La vitesse de rotation des deux corps étant différente, ces moteurs nécessitent deux arbres concentriques plus longs et plus lourds. En contrepartie, le rendement est nettement amélioré[22].
Les deux arbres tournent généralement dans le même sens, afin de ne pas imposer aux roulements (ou paliers) les reliant, des vitesses de rotation trop importantes. Dans certains cas toutefois, ils tournent dans des sens différents, ce qui a pour avantage de ne pas cumuler les couples gyroscopiques, et de permettre un meilleur rendement aérodynamique. Par contre, l'excitation dynamique qui résulte de deux corps contra-rotatifs est fonction de la somme des régimes de rotation des deux corps — au lieu d'être fonction de la différence des régimes, dans le cas co-rotatif — donc très élevée, ce qui pose des problèmes de tenue aux vibrations[27].
Tous les moteurs de nouvelle génération sont à double corps, voire à triple corps pour ceux à très fort taux de dilution. Cette dernière configuration est une spécificité de la famille de moteurs Rolls-Royce "Trent" pour l'aviation civile.
Turboréacteur « simple flux »
![]() |
![]() | |
L'Honeywell ALF 502 (en) est un turboréacteur double flux et double corps installé sur le Bombardier Challenger 600-1A11. |
Dans ce type de machine tout le débit d'air passe dans le générateur de gaz. Ce type de turboréacteur est 'mono-corps, c'est-à-dire qu'il n'y a qu'un attelage compresseur-turbine. La poussée produite dépend de la masse d'air pénétrant dans le générateur de gaz et de l'accélération donnée à celle-ci. Le point de fonctionnement de ce type de turboréacteur est essentiellement caractérisé par la vitesse de rotation de l'ensemble compresseur-turbine et de la température entrée turbine.
Domaine d'utilisation
Les turboréacteurs à simple flux sont bruyants, polluants et ont une consommation spécifique élevée. Ils n'atteignent leur meilleur rendement qu'au-delà de Mach 1.
En raison de son rendement et de sa consommation, le turboréacteur Simple Flux est surtout utilisé pour les grandes vitesses de vol et dans le domaine militaire. Ces moteurs peuvent être équipés de post-combustion pour une grande augmentation de poussée sur de courtes périodes.
Turboréacteur « double flux »
Dans ce type de turboréacteur, on admet plus d'air qu'il n'est nécessaire au générateur de gaz afin de réduire la consommation de carburant et d'augmenter le rendement de propulsion. Le débit (ou flux) supplémentaire s'écoule en dérivation autour du générateur de gaz.
Bien plus économiques aux vitesses subsoniques et moins bruyants, les turboréacteurs à double flux sont apparus dans les années 1960. Dans ces moteurs une soufflante de grande dimension permet d'absorber un gros débit massique qui ne passe qu'en partie dans le compresseur BP. L'air pré-comprimé par la soufflante qui ne passe pas dans le compresseur BP, appelé flux froid, contourne la partie chaude jusqu'à la tuyère où il est éjecté, mélangé ou non avec les gaz chauds (flux chaud)[25]. Cela permet, pour des vitesses modérées, en dessous de Mach 1,5 environ, d'augmenter la poussée par augmentation du débit de gaz, et de réduire considérablement le niveau de bruit[26]. Dans de rares cas, comme sur le General Electric CF700 (en), la soufflante n'est pas placée à l'avant du moteur, mais à l'arrière.
La proportion d'air constituant le flux froid qui est variable selon les moteurs est exprimée par le rapport du débit massique secondaire (ou flux froid) au débit massique primaire (ou flux chaud). Ce rapport est appelé taux de dilution. Les moteurs militaires optimisés pour le vol supersonique ont des taux de dilution inférieurs à 1, alors que les moteurs civils ou militaires optimisés pour des croisières autour de Mach 0,8, ont des taux de dilution entre 5 et 10[22],[26]. Les moteurs à double flux et fort taux de dilution tirent l'essentiel de leur poussée du flux froid (80 %), le flux chaud représentant 20 % de la poussée, et se rapprochent des turbopropulseurs[26].
Avantages et domaine d'utilisation
Le développement des turbopropulseurs, et des réacteurs double flux munis d'une très large soufflante s'est largement développé pour les domaines de vitesse subsonique. Avec un débit d'air plus élevé et une température des gaz plus basse pour une même poussée, leur rendement est plus élevé et leur consommation plus faible. La charge en carburant étant diminuée, cela permet une charge utile supérieure.
Le rendement de propulsion qui est le rapport de la puissance nécessaire au vol et de la puissance thermique produite fait apparaitre pour une poussée donnée que ce rendement serait d'autant plus élevé que le débit d'air serait lui aussi plus élevé : la solution qui consisterait à augmenter le débit d'air sans augmenter le débit carburant serait de ce fait acceptable or il n'en est rien car cela a pour conséquence de diminuer le rendement thermique. Donc pour augmenter le débit d'air sans diminuer le rendement thermique, une solution s'impose : partager le débit d'air total en deux flux :
- un flux pour le générateur de gaz pour conserver un rendement thermique optimum ;
- un flux s'écoulant en dérivation et mélangé au flux chaud soit dans la tuyère, soit dans l'atmosphère.
Le double flux réalise un compromis entre le turboréacteur simple flux dont le rendement n'est intéressant qu'à vitesse élevée et le turbopropulseur limité en vitesse. Par ailleurs la consommation spécifique est améliorée et le fonctionnement moins bruyant. La post-combustion est néanmoins possible avec un rendement plus élevé que dans le cas du simple flux.
Sous-systèmes du turboréacteur
Circuit d'air Interne
Dans un turboréacteur double flux, l'air servant à la pressurisation des joints labyrinthes est prélevé en aval du compresseur basse pression. L'air de refroidissement des parties chaudes comme les distributeurs et les aubes de turbine HP est prélevé en sortie du compresseur HP. Le circuit d'air interne permet aussi d'exercer des contre-pressions sur les disques de compresseur et de turbine afin de diminuer les forces axiales sur les paliers. Afin de conserver un rendement suffisant on limite les fuites d'air en disposant des joints labyrinthes tout au long du moteur. Un contrôle actif des jeux entre les rotors et les carters des compresseurs et turbines est assuré par l'envoi d'air prélevé et contrôlé par une vanne elle-même commandée par la régulation du moteur.
Circuit d'air externe
Dans un turboréacteur double flux le circuit d'air externe assure des fonctions diverses sur le moteur lui-même et sur l'avion. L'air est généralement prélevé sur le compresseur HP et peut être utilisé :
- sur le moteur :
- pour le dégivrage de l'entrée d'air,
- pour éviter le pompage compresseur grâce à une vanne de décharge,
- pour servir comme informations de pression et de température pour la régulation du moteur ;
- sur l'avion :
- pour la pressurisation et la climatisation de la cabine,
- pour le dégivrage de la voilure,
- pour la pressurisation de certains réservoirs (hydraulique, eau, carburant),
- pour le démarrage des autres moteurs.
Certains accessoires, qui subissent un échauffement important, sont refroidis par circulation d'air et la ventilation de la nacelle moteur est réalisée à partir du flux secondaire ou de l'air extérieur.
Circuit d'huile
La lubrification consiste à assurer l'établissement et le renouvellement du film d'huile sur les pièces nécessitant un graissage, telles que les paliers, ainsi que l'évacuation des calories. Les huiles utilisées dépendent des conditions de charges et de températures et sont actuellement majoritairement d'origine synthétique à cause de leur plus grande plage de température et de leur plus grande durée de vie que les huiles d'origine minérale.
Le circuit d'huile assure les fonctions de :
- stockage ;
- alimentation sous pression ;
- filtrage ;
- récupération ;
- refroidissement ;
- dégazage ;
- contrôle de fonctionnement par mesure de pression et de température ;
- contrôle d'usure par bouchon magnétique ;
- contrôle de colmatage des filtres.
Fonction de démarrage
La fonction de démarrage doit assurer :
- le lancement de l'attelage compresseur-turbine ;
- l'alimentation en carburant durant la phase de démarrage ;
- la commande des bougies d'allumage de la chambre de combustion.
Lancement
Cette fonction consiste à entrainer en rotation l'ensemble tournant du générateur de gaz afin que le compresseur puisse alimenter en air la chambre de combustion. Le couple (C) nécessaire à l'entrainement est fonction de la vitesse de rotation et de la température. Au début il croît fortement et diminue lorsque l'allumage se produit et que la machine accélère. À partir d'un certain régime ce couple devient nul et le moteur est dit autonome.
Alimentation en carburant
Cette fonction commande l'alimentation des injecteurs principaux et de démarrage. Les injecteurs de démarrage permettent la propagation de la flamme et l'allumage du carburant pulvérisé par les injecteurs principaux. L'alimentation en carburant est faite sous pression à l'aide d'une pompe et le débit nécessaire au démarrage est déterminé par un dispositif de dosage spécifique.
Allumage
Cette fonction permet de réaliser l'inflammation du mélange carburé à l'aide d'étincelles produites par des bougies haute tensions.
Cycle de démarrage
Ce cycle est caractérisé par l'évolution des paramètres :
- température des gaz ;
- vitesse de rotation ;
- accélération.
La séquence de démarrage est réalisée par une fonction spécifique dédiée du turboréacteur.
Rallumage en vol
La procédure de rallumage en vol est différente de l'allumage au sol par le fait que le lancement est déjà réalisé et que cette procédure doit être réalisée dans une plage déterminée par la vitesse de vol et l'altitude.
Ventilation
Il est parfois nécessaire au sol et dans le cadre d'essais ou de procédure particulière de réaliser le lancement de l'attelage compresseur-turbine sans allumage et avec ou sans injection de carburant. La ventilation sèche peut être utilisée :
- pour évacuer le carburant non brûlé avant un démarrage ;
- pour le refroidissement de la température résiduelle afin d'éviter les points chauds après un essai ;
- dans le cadre de procédure de maintenance ;
La ventilation humide peut être utilisée après essais pour le stockage des moteurs avant leur installation sous l'aile.
Commande et régulation
Commande

La commande d'un turboréacteur par le pilote s'effectue par un moyen simple, en général une commande unique appelée manette des gaz. L'objectif est d'obtenir pour une position donnée de la manette des gaz les performances de poussée adaptées aux conditions de vol. La pression, la température et la vitesse de l'air admis dans le moteur variant en permanence avec l'altitude et la vitesse de vol, il a été nécessaire d'interposer entre la commande pilote et le moteur un système de régulation.
Les positions caractéristiques de la manette des gaz pour un turboréacteur civil sont :
- TO/GA (Take-off/Go around - Décollage/Remise de gaz) ;
- CL (Climb - Montée) ;
- Mct (Maxi continu) ;
- Idle (Ralenti) ;
- Rev (Reverse - Inverseur de poussée).
Contrôle
On sait que la poussée est fonction du débit d'air qui entre dans le turboréacteur et de sa vitesse d'éjection en sortie. On peut dire, en première approximation, que le débit d'air est proportionnel à la vitesse de rotation et que la vitesse d'éjection est proportionnelle à la température devant la turbine. En conséquence contrôler la poussée revient à contrôler :
- le régime de rotation
- la température devant turbine
La fonction contrôle a en outre pour objet :
- de s'assurer que les limites de fonctionnement ne sont pas dépassées ;
- de déceler une anomalie éventuelle de fonctionnement ;
- de suivre en temps réel les divers paramètres moteurs ;
- de contrôler certaines phases de fonctionnement comme le démarrage.
Cette fonction est réalisée à partir de mesures effectuées sur des paramètres comme :
- le régime de rotation ;
- la température des gaz ;
- les pressions pneumatiques et hydrauliques relevées en divers endroits ;
- les températures air, huile, etc.
la mesure des vibrations au niveau des paliers est essentielle en termes de surveillance pour la sécurité du vol
Régulation
Rôle
La fonction de régulation a pour objectif essentiel de maintenir automatiquement le turboréacteur dans des limites déterminées de vitesse de rotation et de température turbine. Cette régulation agit sur le seul paramètre physique généralement disponible : le débit carburant injecté dans la chambre de combustion.
Constitution
Le système de régulation est constitué de différents équipements qui doivent assurer des fonctions :
- d'information ;
- de transmission ;
- de commande ;
- de génération de puissance.
Ces équipements sont les constituants du circuit carburant, des commandes d'organes mobiles (tuyère, vannes de décharge, stators variables, etc.), du circuit électrique, des différents capteurs et du calculateur de régulation.
Fonctionnement
La régulation en fonctionnement stabilisé d'un turboréacteur maintient un régime de rotation et une température optimale devant turbine afin que la poussée correspondant à la position manette choisie soit fournie quelles que soient les perturbations extérieures. Elle maintient de manière automatique le point de fonctionnement correspondant par l'optimisation du couple (débit-carburant ; section de tuyère) en assurant aussi la gestion des limitations de fonctionnement de la machine.
La régulation directe de la température devant turbine étant très délicate, on choisit de réguler des paramètres moteurs représentatifs de cette température :
- régime moteur ;
- régime moteur plus section de tuyère ;
- régime moteur plus température de sortie des gaz ;
- richesse C/P de la combustion avec C pour le débit carburant et P pour la pression en sortie compresseur.
Pour agir sur ces paramètres et les contrôler on dispose de moyens appelés [paramètres réglants] en nombre variable suivant le type de turboréacteur :
- débit SEC ;
- débit PC ;
- section de tuyère variable ;
- vannes de décharges ;
- stators variables ;
- etc.
Lois de fonctionnement moteur
Des lois de fonctionnement invariables et propres à chaque type de turboréacteur relient ces différents paramètres et permettent à la régulation de maintenir stable le point de fonctionnement moteur correspondant à la poussée choisie par le pilote. Les lois de fonctionnement moteur sont les relations qui permettent de connaître les variations des paramètres réglés ou régulés (ceux que l'on veut contrôler) lorsque varient les paramètres réglants. Ces lois moteur sont des caractéristiques intrinsèques du moteur et sont variables avec les conditions de vol et la valeur des paramètres réglants. Elles ne doivent pas être confondues avec les lois de régulation.
Par exemple pour un réacteur à tuyère fixe, sans stators variables ou sans vannes de décharge, et pour une condition de vol donnée :
- la loi de régulation (régime fonction du débit carburant) va donner la valeur de régime N0 correspondant au débit carburant C0 ;
- la loi moteur (température entrée turbine fonction du régime) donnera la valeur de température entrée turbine Tet0 pour la valeur de régime N0.
Par cet exemple simple l'on voit que la régulation d'un turboréacteur sera l'intégration de ses caractéristiques intrinsèques dans un système plus global tenant compte d'éléments extérieurs.
Pour fixer le point de fonctionnement du moteur, on doit agir sur les paramètres réglants à travers une fonction de régulation qui peut être :
- une régulation programmée dont la valeur de sortie, résultat du traitement de la consigne d'entrée par la loi de régulation, ne tient pas compte des conditions réelles du moment ;
- une régulation de boucle qui tient compte de son action pour modifier celle-ci en fonction des variations extérieures.
Modes de régulation
Il existe deux modes principaux qui peuvent être associés et qui sont les modes :
- programmés ;
- bouclés.
Régulation programmée
Ce type de régulation est stable mais peu précise car les perturbations réelles sont souvent différentes, voire très différentes, des conditions programmées du moment. Le paramètre réglé n'aura pas toujours la valeur désirée et cela recale définitivement ce type de régulation pour garantir la stabilité du point de fonctionnement en fonction des conditions extérieures.
Par exemple, si à une altitude donnée une position manette fixe une valeur de débit carburant qui va elle-même fixer une valeur de régime et que l'altitude change sans que la régulation en soit informée, il va se produire un écart entre le régime réel et le régime qu'il faudrait avoir.
Par contre en régime transitoire, là où les limitations risquent d'être atteintes il est préférable d'utiliser un programme qui intégrera toutes les butées en tenant compte des écarts entre moteurs et du vieillissement des pièces à durée de vie limitée. Par exemple pour un chasseur embarqué, le temps d'établissement de la poussée maximum est souvent aussi important que le niveau de poussée lui-même, car en cas d'appontage raté la remise des gaz doit se faire en toute sécurité sans que le moteur subisse une perte de puissance liée à un pompage ou une extinction riche.
Régulation bouclée
Le principe d'une régulation bouclée est de détecter l'écart entre la valeur de sortie et la consigne d'entrée puis d'utiliser cet écart pour commander un ou plusieurs paramètres réglants. Ce type de régulation permet de s'affranchir des variations extérieures mais présente le défaut d'être instable. Cette instabilité est liée aux temps de réponse des transmissions et au gain de boucle c'est-à-dire au rapport qu'il y a entre la variation de sortie et la variation à l'entrée. Les performances de la boucle seront celles de l'ensemble régulation + moteur, ce dernier ayant ses propres gains et temps de réponse. Les caractéristiques du turboréacteur variant dans des proportions très importantes en fonction des conditions de vol (Mach, Altitude) il faudra donc, pour conserver une bonne réponse de l'ensemble quelles que soient les conditions extérieures, que les caractéristiques du régulateur varient également. C'est ce qui complique les régulations des turboréacteurs par rapport aux régulations de processus industriels.
Régimes de régulation
L'utilisation du turboréacteur consiste à le maintenir en fonctionnement stabilisé pour chaque condition de vol et le faire fonctionner en régime transitoire entre deux états stables. Cela montre la nécessité de prévoir deux modes principaux de régulation :
- une régulation en régime stabilisé qui maintient le point de fonctionnement pour la condition de vol choisie, en dépit de variations éventuelles des conditions extérieures et qui garantit le respect des limites de sécurité pour éviter :
- le départ en survitesse,
- le phénomène de surchauffe,
- etc.
- La régulation en régime transitoire qui permet de changer rapidement de point de fonctionnement en évitant :
- le phénomène de pompage ;
- une extinction du réacteur ;
- le phénomène de surchauffe.
D'autres fonctions sont aussi gérées par le système de régulation :
- le démarrage du réacteur :
- l'allumage des bougies au démarrage :
- le contrôle actif des jeux pour certains moteurs ;
- etc.
Régulation du moteur
Le point de fonctionnement stabilisé d'un moteur se trouve sur une ligne particulière du champ compresseur, mais lorsque le pilote demande un régime compresseur différent à l'aide de sa manette des gaz la régulation doit :
- augmenter le débit-carburant lorsque le pilote accélère ;
- diminuer le débit-carburant en cas de demande contraire et ceci en tenant compte des limitations de la machine.
Pendant les variations de régime, le point de fonctionnement du compresseur quitte la ligne de fonctionnement stabilisé du champ compresseur. Physiquement, une augmentation de carburant dans la chambre de combustion produit une sur-dilatation de l'air d'où une montée brutale du taux de compression du compresseur : le travail produit par la turbine augmentant plus vite que le travail absorbé par le compresseur, le moteur accélère. L'inverse se produit en cas de diminution de carburant, le moteur décélère.
La régulation du moteur fournit donc le carburant nécessaire en fonction du régime de rotation, de la pression et de la température en certains points du turboréacteur.
Limitations et Interdictions
Pour passer d'un point de fonctionnement à un autre, on s'écarte de la courbe stabilisée initiale et l'on se heurte à des limitations :
- une brusque augmentation du débit carburant peut conduire :
- à une surtempérature transitoire devant turbine,
- à une extinction riche,
- au pompage du compresseur par élévation brutale de la pression en sortie compresseur ;
- une diminution du débit carburant pouvant conduire à une extinction pauvre.
Pour se protéger de ces phénomènes dangereux la régulation possède une limitation de débit carburant :
- haute appelée : butée d'accélération :
- basse appelée : butée de décélération.
Préambule
Tous les régulateurs sont constitués d'un système dédié au calcul des lois et d'un autre à leur exécution (débit carburant et géométrie variable). Si depuis les premiers turboréacteurs la partie exécution a peu varié (le système "Doseur-Soupape régulatrice" existait sur l'ATAR101 SNECMA en 1949), une évolution considérable a été réalisée sur la partie calcul.
Jusqu'en 1970 le calcul des Lois est réalisé par des systèmes hydromécaniques mettant en action des leviers, cames, capsules anéroïde, servo-moteurs, réducteurs de pression, etc.
À partir des années 1970, l'électronique apparaît progressivement, c'est l'époque des systèmes de calcul mixtes à "faible autorité" ou les lois de régulation sont en partie réalisées par des fonctions électroniques analogiques avec :
- détection électrique des paramètres moteurs ou des conditions de vol (altitude, pression d'impact, etc.) ;
- asservissements hydromécaniques à consigne électrique.
Vers le milieu des années 1980, la technologie numérique ayant évoluée, apparaissent les premiers systèmes ou l'électronique associée à l'informatique prend complètement en charge la fonction calcul qui traite alors non seulement des lois de régulation mais aussi des lois de protection moteur, de la maintenance intégrée et de la sûreté de fonctionnement de l'ensemble du moteur.
Les régulations qui ont d'abord été hydromécaniques ont évolué vers la mixité avec une part de plus en plus importante de l'électronique pour actuellement être des systèmes dit "Pleine Autorité" et "redondants" ce qui signifie une autonomie complète pour le fonctionnement du moteur et la détection de panne avec reconfiguration sans intervention du pilote.
Évolution technologique
La régulation du moteur ATAR9C SNECMA entièrement hydromécanique avec de l'huile pour fluide précède celle du moteur ATAR9K50 SNECMA qui est équipée d'un système à fuite variable commandé par un moteur électrique pilotant la régulation hydromécanique de tuyère. Sur les moteurs Rolls-Royce/Snecma Olympus-593 du Concorde fut installé le premier système de régulation analogique. Le moteur SNECMA M53-5 fut équipé d'une régulation "Analogique Pleine Autorité" puis le moteur SNECMA M53-P2 fut équipé d'une régulation "Numérique Pleine Autorité".
Depuis le milieu des années 1980 la régulation Numérique Pleine Autorité Redondante a commencé à équiper les Pratt & Whitney PW2000 et CFMI/CFM56-A. Ce système s'est généralisé sur les avions commerciaux de toutes tailles. C'est également le cas de la totalité des avions militaires récents[28].
Régulation du régime
But
La régulation de ce paramètre moteur a pour objectif d'éviter les régimes de sur-vitesse et de sous-vitesses tout en permettant un pilotage précis du niveau de poussée désiré.
Historique
Les premières régulations fonctionnaient sur le même principe que les régulateurs à boules des premières machines à vapeur. La déformation du parallélogramme, fonction du régime, était utilisée pour agir sur le débit carburant. Une action sur la commande des gaz permettant de fournir une nouvelle consigne de régime en modifiant le point d'équilibre du parallélogramme.
Les inconvénients de ce type de régulation étaient de deux ordres :
- un rapport (gain de boucle) fixe entre l'écart de régime détecté et l'écart de débit carburant généré, or en altitude ce rapport (gain) doit diminuer pour éviter le sur-régime :
- un écart de débit carburant proportionnel à ce même gain sur un échelon (mouvement rapide) manette alors qu'il aurait dû être proportionnel à la pression qui règne dans la chambre de combustion pour ne pas faire décrocher le compresseur ou avoir une extinction.
Dans un premier temps ces inconvénients ont été supprimés par une correction du gain de la chaine de retour en y intégrant des capsules barométriques et des amortisseurs mécaniques afin de conserver un gain fort en contre-réaction. Ce type de régulation équipait les moteurs Marboré de Turbomeca équipant les avions Fouga. Malgré ces correctifs, les variations rapides de position manette étaient prohibées au-dessus de 15 000 pieds, afin d'éviter les inconvénients décrits ci-dessus.
Par contre, ce système permet une régulation sans manette des gaz. Ce procédé est employé sur le TURMO IIIC4 de Turbomeca équipant le SA330 Puma. La vitesse du rotor (NR) étant désirée constante, la vitesse de rotation de la turbine (mécaniquement liée au rotor) permet de détecter une variation du NR à la suite d'une variation de la commande de pas collectif. La vitesse de rotation de la turbine (NTL) est appliquée à un système de doseur à masselotte qui modifie le Qc (débit carburant) afin de conserver NTL constant et donc NR constant. Ce système induit une régulation a posteriori. Si le pilote modifie l'équilibre Puissance moteur fournie / Puissance absorbée par le rotor, le régime rotor évolue, la régulation détecte cette variation et corrige le débit carburant afin de retrouver le NR souhaité. Cette régulation est assez molle et toujours par défaut : lorsque le NR baisse, le Qc est augmenté mais insuffisamment pour récupérer le NR d'origine. Inversement, si le Nr augmente, le Qc est diminué mais le nouveau Nr régulé sera supérieur à l'ancien. Ce système a fait ses preuves et est toujours en service car il jouit d'une grande simplicité et donc d'une grande fiabilité, indépendante de toute source électrique.
Dans un deuxième temps le paramètre piloté n'a plus été le débit carburant mais la richesse du mélange air-carburant afin d'éliminer l'influence de la pression donc de l'altitude. Cette régulation a nécessité un mécanisme plus complexe qui permettait d'intégrer des butées hautes et basses sur la variation de la richesse afin de supprimer les limitations sur la vitesse de la manette. Les moteurs ATAR SNECMA ont été les premiers équipés par ce système plus performant.
La connaissance approximative du paramètre richesse à partir du débit carburant et de la pression est améliorée par l'introduction du paramètre Température puis les conditions de vol (altitude, pression d'impact) sont utilisées dans la détermination des butées hautes et basses de la richesse. Toutes ces informations apparaissent sur les moteurs ATAR 9K50 SNECMA sous forme électriques.
Sur les moteurs double-corps un seul corps est régulé en régime, l'autre suit : par exemple sur les F404 en « SEC » c'est le corps HP qui est piloté alors qu'en « PC » c'est le corps BP
Régulation de tuyère
À venir.
Postcombustion

La postcombustion, parfois dénommée réchauffe, est un système utilisé sur les turboréacteurs équipant les avions militaires et certains avions civils supersoniques pour augmenter la vitesse d'éjection des gaz, ce qui conduit à une augmentation de poussée, permettant d'élargir le domaine de vol. Le principe est d'injecter du kérosène — après la turbine, d'où le terme « post » — dans le flux des gaz avant la sortie par le col de tuyère du réacteur. La combustion de cet apport de carburant se fait à l'aide de l'oxygène résiduel encore présent après la combustion primaire[29].
Rôle de la postcombustion
Dans un turboréacteur, ce qui limite la température dans la chambre de combustion principale ce sont les matériaux constituant l'étage de turbine. La poussée fournie par le turboréacteur est proportionnelle à la vitesse d'éjection en sortie de tuyère qui est elle-même limitée par la température en sortie de la turbine. Pour augmenter la vitesse d'éjection entre la sortie de la turbine et la tuyère d'éjection, on injecte du carburant dans le flux de gaz qui contient encore de l'oxygène du fait de la dilution pour refroidissement dans le cas des moteurs simple flux ou du fait dans les moteurs double flux que le flux secondaire n'a pas participé à la combustion primaire.
Cet apport de puissance supplémentaire permet d'augmenter le domaine de vol et de permettre des missions d'interception. Certaines possibilités comme le décollage sur piste courte ou le dégagement en combat aérien sont possibles grâce à cet équipement. Ce système de réchauffe a équipé à ce jour seulement deux avions civils, le Concorde français et le Tupolev Tu-144 russe. Il reste que, même en étant rendu nécessaire par la limite métallurgique de la turbine, il n'est utilisé que transitoirement, car c'est un gros consommateur de carburant et il reste essentiellement l'apanage des avions de combat rapides[29].
Généralités
Pour éjecter un gaz à travers une tuyère, il suffit que sa pression génératrice amont soit supérieure à la statique extérieure aval. La vitesse d'éjection est une fonction croissante de la pression génératrice jusqu'à une valeur particulière du rapport pression amont sur pression aval. Au-delà la vitesse d'éjection reste constante.
Le débit massique et le débit de quantité de mouvement à travers la tuyère n'ont pas de limite et augmente comme la pression génératrice. La vitesse limite d'éjection dépend de la température du gaz : plus le gaz sera chaud, plus la vitesse d'éjection sera élevée.
Si la température augmente, pour une pression génératrice donnée le débit massique éjecté décroît mais la quantité de mouvement éjectée augmente et donc la poussée augmente. De ce fait on peut augmenter la poussée d'un turboréacteur donné caractérisé par une pression génératrice maximale de son plein gaz « SEC » en réchauffant le gaz avant son éjection.
Ce réchauffage s'appelle post-combustion ou réchauffe et le point de fonctionnement moteur le plein gaz « PC ».
Particularités
Avantages
C'est un moyen techniquement simple, car sans pièces mécaniques mobiles supplémentaires, qui le rend léger et exempte des contraintes thermiques auxquelles sont soumises les autres parties du moteur. Il permet une augmentation de la poussée [+ 50 %] d'un turboréacteur sans modification de sa taille ni du fonctionnement de son compresseur. C'est un moyen nécessaire pour atteindre les Mach élevés lorsque la tuyère ne peut être adaptée en permanence aux caractéristiques du vol.
Inconvénients
Pour les militaires, la « PC » présente une signature infrarouge importante et augmente nettement la consommation spécifique (CS en kg/daN/heure) du moteur. Pour les civils, le bruit et la CS sont des inconvénients majeurs.
Enfin, l'apparente simplicité mécanique n'écarte pas l'obligation d'avoir une tuyère à section de col variable, afin d'éviter une augmentation de la pression de sortie du compresseur en amont de la réchauffe. Cette augmentation de pression, appelée blocage thermique, risquerait de faire décrocher le compresseur.
Augmentation de la poussée
Pour un débit gazeux D éjecté à la vitesse Vs, d'une tuyère adaptée de section de col Sc et de section de sortie S les formules d'aérodynamique indiquent que le nombre de Mach en sortie de tuyère est strictement lié au rapport des sections de col et de sortie ainsi qu'au rapport (Cp/Cv) de la chaleur massique de l'air à pression constante sur la chaleur massique de l'air à volume constant.
La poussée est proportionnelle au Mach en sortie de tuyère et à la vTt (Température totale du gaz). Dans un turboréacteur le débit étant fixé par le compresseur, si on maintient constante la géométrie de tuyère on rend la poussée uniquement dépendante de la Température totale du gaz. On obtient alors la formule simplifiée F ˜ vTt
Exemple : si Tt = 1 000 K au PG sec et si Tt = 2 000 K au PGpc alors le rapport de poussée entre le PGsec et le PGpc est de v2 = 1,414
Augmentation de la vitesse des gaz
La conservation du débit entre l'entrée et la sortie associée à la dilatation des gaz par son réchauffement conduisent à augmenter la vitesse en sortie proportionnellement au rapport de dilatation si on prend un conduit cylindrique et un écoulement subsonique.
Inverseur de poussée

But
C'est un système (avions de transport, ravitailleurs, etc.) qui équipe certains avions de combat comme le Panavia Tornado ou le Saab 37 Viggen mais qui est monté principalement sur les avions civils commerciaux équipés de réacteurs. Cet équipement qui n'est pas obligatoire sur ce type d'avion n'est pas pris en compte dans la certification d'un appareil. Sur les gros porteurs commerciaux ou militaires, c'est un système qui a pour objectif de créer une poussée vers l'avant afin de réduire la distance de roulage en soulageant le système de freinage.
Principe
L'inversion de poussée est un dispositif qui consiste à introduire un obstacle dans l'écoulement afin d'en dévier une partie dans le sens du roulage et de ce fait créer une poussée négative qui tend à ralentir l'appareil dans la phase de roulage qui suit le posé du train afin de réduire les distances de freinage lors de l'atterrissage. Sur les moteurs double-flux, l'inversion peut se faire sur les deux flux, la contre-poussée obtenue étant la différence entre la poussée négative obtenue sur le flux secondaire et la poussée du flux primaire. Généralement seul le flux secondaire est dévié par les dispositifs d'inversion[30].
Technologie

Plusieurs types d'inverseurs sont utilisés comme :
- les inverseurs à grille sur le flux secondaire des moteurs CFM ;
- les inverseurs à grille sur les deux flux sur les moteurs type CF650 ;
- les inverseurs à obstacle comme sur concorde où deux parties symétriques de la tuyère pivotent pour renvoyer le jet vers l'avant.
L'inverseur ne peut se déployer qu'une fois l'avion au sol et des systèmes de sécurité redondants empêchent toute ouverture ou déploiement de celui-ci en vol. L'inverseur est commandé par des manettes spécifiques équipant la commande des gaz.
Poussée vectorielle
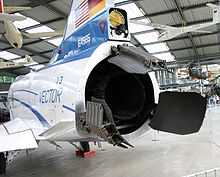
Spécificité des avions militaires les plus performants, notamment les intercepteurs, la tuyère des réacteurs est prolongée par un dispositif orientable permettant de dévier le jet et donc la direction de la poussée pour augmenter la manœuvrabilité de l'appareil. On parle généralement de poussée bidimensionnelle (respectivement tridimensionnelle) lorsque la poussée est dirigée dans un (respectivement deux) plan directionnels. Outre cet aspect, elle permet aussi de se déplacer dans des milieux où les ailerons et les gouvernes sont inutiles, c'est-à-dire à très haute altitude où l'air est raréfié[31].
Ce dispositif équipe notamment des prototypes russes Soukhoï (SU-37, MiG 1.44 et MiG-29 OVT) et des chasseurs américains (F-22, F/B-22 Concept et JSF). Le plus récent développement (2005) est le Rockwell-MBB X-31. La poussée peut aussi être déviée vers le sol afin de permettre les décollages et atterrissages verticaux, comme sur le Harrier, le F-35 et le Yak-141[31].
Nacelle
Sous la dénomination de nacelle on identifie l'ensemble des capotages qui enveloppent le moteur et sa suspension à l'aile ou au fuselage de l'avion.
Les fonctions principales d'une nacelle sont :
- assurer les écoulements d'air à l'extérieur et au travers du moteur avec de bonnes performances aérodynamiques et acoustiques ;
- contenir les accessoires du moteur, voire de l'avion ;
- guider les ventilations nécessaires au moteur et à ses accessoires avec de bonnes étanchéités ;
- contenir un incendie éventuel ou assurer la rétention d'une aube de soufflante qui se détacherait ;
- assurer parfois l'inversion de poussée du moteur.
Groupe auxiliaire de puissance

Les turboréacteurs nécessitent généralement l'aide d'un moteur auxiliaire pour être démarrés, le GAP (groupe auxiliaire de puissance) ou APU (Auxiliary Power Unit). Il s'agit d'un petit turbomoteur, souvent dérivé d'une turbomachine d'hélicoptère et situé dans le fuselage de l'aéronef, souvent dans la partie arrière, qui fournit l'air comprimé pour alimenter les démarreurs pneumatiques des turboréacteurs, ainsi que l'énergie électrique avant les démarrages. Le GAP peut parfois servir à la génération hydraulique, en secours[32].
Le GAP est démarré par la ou les batteries électriques de l'avion, ou par un groupe de puissance extérieur. Le GAP peut aussi être utilisé en générateur électrique de secours, lorsque toutes les génératrices et alternateurs des turboréacteurs ou turbopropulseurs sont inopérants. Des essais récents ont été menés avec succès avec des piles à hydrogène en tant que GAP. Ces dispositifs sont plus légers et ne nécessitent pas d'entrée d'air, mais ils sont plus onéreux[32].
Applications et fabricants

Probablement moins connu du grand public, les turboréacteurs trouvent quelques applications sur les véhicules terrestres. Le Thrust SSC, véhicule terrestre supersonique détenteur du record absolu de vitesse au sol avec une moyenne à 1 227,985 km/h, est propulsé par deux turboréacteurs à postcombustion développant une puissance d'environ 106 000 ch[33]. Des versions turbo-motorisées des dragsters, dénommées jet-cars, existent également, mais celles-ci ne peuvent participer à aucun championnat et ne font l'objet que de démonstrations.
En raison de leur capacité à atteindre des vitesses transsoniques (entre mach 0,8 et mach 1) de manière économique, les turboréacteurs sont essentiellement utilisés sur des aéronefs aussi bien militaires que civils. Tous les avions de plus de 110 places, ceux produits par Airbus et Boeing, sont équipés de turboréacteurs. Trois grands fabricants équipent ces avions, à savoir les américains General Electric et Pratt & Whitney, et le britannique Rolls-Royce. On peut y ajouter quatre autres sociétés : le français Snecma, l'allemand MTU Aero Engines, l'italienne Avio et le japonais JAEC (en), qui participent à la production de réacteurs en association avec les « trois grands »[34].
Ainsi, Snecma intervient en association avec General Electric au sein de CFM International, une coentreprise détenue à parité égale, pour équiper essentiellement les Airbus de la famille A320 et les Boeing 737. De même, JAEC et MTU Aero Engines participent également à une société commune, International Aero Engines, avec Rolls-Royce et Pratt & Whitney. International Aero Engines est détenue à hauteur de 32,5 % par Rolls-Royce, 32,5 % par Pratt & Whitney, 23 % par JAEC et 12 % par MTU. Elle fabrique des réacteurs destinés exclusivement aux Airbus de la famille A320. Enfin, General Electric et Pratt & Whitney se sont associés dans une coentreprise détenue à parité, Engine Alliance, pour équiper l'Airbus A380, en concurrence avec Rolls-Royce[34]. Le 10 février 2011, Avio a signé un accord industriel avec le motoriste aéronautique américain Pratt & Whitney pour la fourniture de son nouveau moteur Pure Power PW1500G.
Développement et certification
But
L'ensemble des activités liées au développement d'un turboréacteur et à sa certification ont pour objectif de démontrer qu'à son entrée en service il remplira les conditions de qualité et de sécurité imposées par le client, en l'occurrence l'avionneur. L'aspect qualité sera traité par les essais de développement tandis que les critères liés à la sécurité seront évalués lors des essais de certification.
Essais de développement
Les essais de développement qui ont pour objectifs d'optimiser les performances et d'acquérir des données d'ingénierie portent principalement sur :
- le domaine de fonctionnement des composants principaux tels que ;
- le FAN ;
- les compresseurs HP et BP ;
- les turbines HP et BP ;
- la chambre de combustion ;
- les performances globales de la machine au fur et à mesure de l'assemblage des différents composants jusqu'au moteur complet ;
- l'opérabilité qui permet de vérifier le comportement en transitoire (marges au pompage) et de déterminer les butées de fonctionnement (accélération et décélération) ;
- les ventilations internes, les contraintes mécaniques et la pollution sonore et chimique ;
- l'endurance qui permet de valider certains choix technologiques ;
- l'ingestion d'objet (oiseaux, glace, eau, sable) et le givrage ;
- la préparation des essais en vol et au sol sur des bancs d'essai globaux à l'air libre et fermés.
Pour assurer le développement d'un nouveau moteur il fallait dans les années 2000 :
- 7 à 8 moteurs de compliance dérivés des prototypes et similaires au moteurs qui seront produits en série ;
- une durée totale de 3 ans (18 mois pour un moteur dérivé) et un budget conséquent ;
- environ 5 000 heures de fonctionnement accumulées à la certification.
Certification
Le développement et la fabrication des turboréacteurs utilisés pour motoriser des aéronefs doivent répondre aux exigences d'organismes tels que la DGAC (JAR-E) pour la France ou la FAA (FAR33) pour les États-Unis. Certains constructeurs comme la SNECMA pour la France et GE pour les États-Unis coopèrent sur des moteurs communs ce qui les obligent à satisfaire à la norme la plus contraignante en cas de désaccord.
La certification se fait en deux grandes étapes :
- par démonstration ;
- similarité par rapport à un existant déjà certifié ;
- analyse technique et méthodologique ;
- résultats d'essais partiels ;
- résultats d'essais moteur complets ;
- par des essais moteurs qui permettent ;
- la calibration des caractéristiques de puissance du moteur ;
- la démonstration de bon fonctionnement (démarrage, ralenti, accélération, survitesse, réponse en poussée) ;
- de vérifier l'absence de vibration et de résonance néfaste dans le domaine de fonctionnement ;
- de tester l'endurance par des essais cyclés ;
- de tester l'absence de feu pendant 15 secondes et l'absence de rupture de la suspension à l'aile du moteur à la suite de la rupture d'une aube FAN ;
- de vérifier la tenue du moteur en cas de dépassement important de la température EGT pendant une durée de plusieurs minutes ;
- de vérifier la tenue au givrage par injection d'eau à basse température ;
- de vérifier la bonne tenue du moteur en cas d'injection (eau, glace, sable, oiseaux).
Contrat avec l'avionneur
Le motoriste signe avec l'avionneur un contrat sous forme de spécifications définissant et garantissant toutes les données techniques du moteur qui sera installé sur l'avion. Ce contrat comporte deux clauses fondamentales :
- une garantie de poussée ;
- une garantie de consommation spécifique.
La démonstration de la capacité du moteur à satisfaire les exigences de poussée et de consommation spécifiques s'effectue à travers le programme de certification avion dont les étapes principales pour le moteur sont les suivantes :
- fonctionnement au sol sur des bancs d'essai ouverts des moteurs de compliance d'abord équipés avec nacelle ATC puis dans un deuxième temps équipés avec nacelle FTC ;
- essais de performance en vol avec nacelle FTC ;
- calcul de la poussée en vol et établissement des lois de conduites (Power Management) ;
- calcul de la consommation spécifique et comparaison avec la garantie.
Poussée et lois de conduite (Power Management)
But
L'établissement des différents réglages du moteur pour les régimes d'utilisation (ralenti sol et vol, décollage, montée, croisière) et la demande de poussée de l'avionneur s'effectue dans tout le domaine de vol et pour chacune des versions du moteur.
Ce processus se fait en trois étapes :
- définition des niveaux de poussée nécessaires ; ;
- démonstration de la capacité du moteur à satisfaire les niveaux de poussée requis tout en restant dans les limites certifiées ;
- détermination des lois de conduite du moteur permettant de satisfaire les niveaux de poussée exigés.
Définition de la poussée nécessaire
L'évaluation de la poussée que devra fournir le moteur est le résultat d'un processus qui démarre chez l'avionneur par des études de marché qui ont pour objectif de définir les besoins des compagnies aériennes en termes de taille, poids, distance franchissable, etc., et qui conduisent à la définition de la classe de poussée de l'ensemble propulsif.
Le motoriste propose à l'avionneur un modèle mathématique du moteur qui intègre son expérience industrielle, les exigences du client et ce que propose la concurrence. À partir de ce modèle et après de nombreuses révisions le motoriste et l'avionneur se mettent d'accord sur une spécification contractuelle qui intègre les garanties de poussée et de consommation spécifique.
Démonstration de la capacité du moteur
Essais au sol en nacelle ATC
Chaque moteur de démonstration (compliance engine) est testé équipé de la même nacelle ATC dans un banc d'essai ouvert (à l'air libre) suivant la même procédure que celle qui sera déroulée pour les futurs moteurs de série :
- test d'étanchéité de la nacelle ATC ;
- rodage du moteur ;
- stabilisation et définition des régimes moteurs.
ces essais serviront de base pour l'établissement des limites de réception des moteurs de série.
Essais au sol en nacelle FTC
Les moteurs de démonstration sont testés avec la nacelle FTC suivant la même procédure qu'avec la nacelle ATC. Les résultats d'essais seront utilisés pour :
- établir les caractéristiques (corrélations de pression) nécessaires au calcul de la poussée en vol ;
- établir les facteurs correctifs entre la nacelle ATC de référence et la nacelle FTC de référence.
Calcul de la poussée en vol
La poussée en vol est calculée car on ne sait pas la mesurer et cela nécessite des moteurs fortement instrumentés. Le principe est de calculer la variation de quantité de mouvement au travers du moteur en s'appuyant sur l'équation d'Euler. Après avoir déterminé les coefficients de tuyère au moyen d'essais maquette et déterminé les corrélations de pression amont et aval du moteur à partir des essais au sol avec nacelle FTC les essais en vol se poursuivent en palier stabilisé (Trainée = Poussée) pour différents régimes.
À partir du calcul de la poussée en vol :
- l'avionneur établi la polaire de son aéronef ;
- le motoriste établi le modèle de son moteur.
Essais en vol
Les essais en vol permettent :
- de collecter les données nécessaires à l'établissement des lois de conduite du moteur ;
- de déterminer les niveaux de SFC afin de les comparer aux niveaux de garantie ;
- d'élaborer un modèle définissant les performances combinées de l'avion et du moteur que l'on proposera au client ;
- de relever les caractéristiques du moteur au décollage (température et régimes) en transitoire.
Établissement des lois de conduite
Cette étape permet d'établir les régimes de pilotage en rapport de la garantie de poussée qui a été vendue à l'avionneur. Pour cela les moteurs de démonstration étant considérés comme des moteurs de série moyen (en performances) les caractéristiques poussée / régimes issues des essais en vol permettent d'y parvenir.
Ces caractéristiques moyennes intègrent :
- la dispersion des moteurs de série (+/- 2 % couramment) ;
- les imprécisions de régulation ;
- les effets de l'humidité de l'atmosphère.
Garantie de consommation spécifique
Définition
La SFC représente la consommation de carburant par unité de poussée et est utilisée pour évaluer l'efficacité du moteur. C'est un critère de conception très important et un moteur est conçu en ayant pour objectif d'optimiser ce paramètre aux conditions de vol les plus courantes, la croisière généralement c'est-à-dire pour une altitude de 40 000 pied et Mach 0,8.
La formule de la consommation spécifique est :

Relation entre SFC et Specific Range
Le critère de S/R permet de corréler la consommation de carburant du moteur avec la vitesse air de l'avion afin de permettre une correspondance entre la poussée du moteur et la vitesse de l'avion.
La formule du S/R est :

D'après la définition de la SFC on peut déduire que WF = FN*SFC
La finesse de l'avion est
Sachant que dans le cas d'un vol stabilisé :
- la poussée des moteurs est égale à la traînée globale (avion + moteurs) ;
- la portance est égale au poids total de l'avion,
on en déduit que la finesse de l'avion est alors :

on en déduit

et
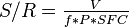
soit à masse et vitesse avion constantes une augmentation de SFC a pour conséquence une réduction du même ordre du S/R
Technologie
Pour les moteurs à taux de dilution élevé, les caractéristiques du cycle thermodynamique qui affectent la SFC sont :
- le rapport de compression global ;
- le taux de dilution ;
- la température de sortie de la chambre à combustion ;
- le taux de compression du Fan ;
- le fait d'avoir un moteur dont les flux chaud et froid sont mélangés ou non avant éjection.
Évidemment le rendement de chaque composant (compresseurs, chambre de combustion, turbines, etc.) affecte également la SFC.
Garantie de SFC
L'estimation initiale des niveaux de SFC d'un nouveau moteur est basée sur un modèle théorique intégrant l'expérience du motoriste sur les modèles déjà en ligne. Le niveau de garantie signé avec l'avionneur est l'aboutissement de nombreuses itérations qui intègrent les offres de la concurrence. Le niveau de garantie vendu par le motoriste est alors utilisé par l'avionneur pour établir les performances de l'avion proposé aux compagnies aériennes.
Comme pour la poussée, la démonstration des garanties de SFC est réalisée pendant le programme de certification de l'avion motorisé avec les moteurs de démonstration. Les résultats des essais en vol (calcul de la poussée et mesure du débit carburant) sont utilisés pour calculer la SFC et ensuite la comparée aux niveaux de garantie initialement vendus.
Le motoriste et l'avionneur se mettent d'accord sur le niveau de performance du moteur qui conditionnera :
- les performances de l'avion ;
- les limites de réception des moteurs de série ;
- les pénalités financières éventuelles à devoir par le motoriste en cas de manquement aux engagements de garantie ;
- la mise en œuvre d'un programme de rattrapage dans le cas d'un déficit par rapport aux garanties.
Équivalent Spec
Le paramètre ÉQUIVALENT SPEC sert à calculer les pénalités financières que le motoriste sera amené à donner à l'avionneur en cas de déficit des garanties sur la SFC. Deux possibilités :
- les garanties sont tenues et il n'y a pas de pénalités ;
- le moteur est déficitaire, il consomme plus que prévu et dans ce cas les limites de réception des moteurs de série sont recalculées en rapport de l'écart à la garantie initiale. Ces nouvelles limites portent le nom de ÉQUIVALENT SPEC.
Le nouveau niveau de SFC est déterminé à partir de la moyenne des moteurs de démonstration à laquelle on retranche le déficit mesuré en vol. Ensuite on calcule le paramètre ÉQUIVALENT SPEC qui est la transposition au sol de la situation des moteurs vis-à-vis de la garantie initiale en vol.
Production et réception
La production des moteurs de série est sanctionnée par un essai de réception défini dans des documents ayant fait l'objet d'accord avec les autorités (FAA, DGAC, etc.) et les avionneurs. Ces documents traitent des aspects sécurité et sûreté de fonctionnement pour une part et d'autre part décrivent dans les moindres détails l'essai de réception ainsi que les limites de réception.
Essais de réception
Préambule
Cet essai qui permet de valider en une seule fois la totalité des versions du moteur qui, lui, n'est livré qu'à sa version de vente, comprend deux phases principales :
- la vérification du bon comportement mécanique ;
- rodage stabilisé ;
- équilibrage et niveaux vibratoires ;
- rodage transitoire ;
- la vérification des performances et des limites garanties pour la totalité des versions du modèle de moteur.
Évaluation des performances d'un moteur
Généralités

Les performances du moteur en essai ne sont pas comparables directement car elles dépendent :
- des conditions ambiantes le jour de l'essai ;
- pression atmosphérique ;
- température de l'air admis par le moteur ;
- humidité de l'air ;
- de l'environnement du moteur en essai ;
- banc d'essai fermé ;
- systèmes d'adaptation complémentaires nécessaires à l'essais (Buse d'entrée, Nacelle d'avionnage, Instrumentation) ;
- du moteur lui-même ;
- influence des lois de régulation et configuration des systèmes variables équipant le moteur en position nominale.
Standardisation
Pour sanctionner les performances d'un moteur, il est indispensable de les ramener à des conditions connues de fonctionnement. La méthode utilisée est de :
- corriger les résultats bruts issus de l'essai par l'utilisation de coefficients de correction dépendants
- des écarts entre les conditions ambiantes du jour de l'essai et les conditions ambiantes standards
- pression atmosphérique 1 013,25 hPa
- température ambiante 15 °C
- humidité 0 %
- des différences existant entre l'environnement d'essai et l'environnement d'utilisation (sur avion) qui est
- moteur intégré dans une nacelle avion et fonctionnant à l'air libre
- sans instrumentation dans la veine d'entrée d'air
- des écarts liés au moteur lui-même et dus à l'action de sa régulation
- des écarts entre les conditions ambiantes du jour de l'essai et les conditions ambiantes standards
- exprimer ces résultats corrigés en fonction d'un paramètre moteur choisi comme référence tel que :
- un régime de référence (paramètre réglant)
- la poussée de référence (paramètre réglé)
Ces corrections sont appliquées sur les paramètres contractuels tels que :
- la poussée ;
- le débit carburant ;
- les régimes des corps BP et HP pour les moteurs double-corps ;
- la température d'entrée turbine, trop élevée pour être directement mesurée, remplacée par la mesure de température des gaz d'éjection appelée EGT.
Les fluctuations sur les performances du moteur au banc d'essai ont plusieurs origines et se répartissent en gros de la manière suivante sur 100 % de variation :
- 40 % sont dues aux mesures physiques réalisées dans le banc d'essai ;
- 30 % sont dues aux corrections apportées par les calculs ;
- 30 % sont liées directement aux aléas de production des moteurs.
Corrections apportées aux résultats bruts d'essai
Correction de pression ambiante
Cette correction permet de ramener la valeur des paramètres de poussée et de débit carburant du moteur en essai à des conditions de pression ambiante standard 1 013,25 hPa afin de les comparer aux limites contractuelles vendues à l'avionneur.
Correction de température ambiante
Cette correction affecte les paramètres de régime de rotation, de température EGT et de débit carburant par des coefficients calculés à partir d'un modèle théorique du moteur et de sa régulation dont on fait varier les conditions de température ambiante dans toute la gamme des températures susceptibles d'être rencontrées en essai de réception.
La qualité de ces coefficients et donc des corrections apportées dépend étroitement de la représentativité du modèle (moteur + régulation) ayant servi à leur détermination. La modélisation du dévrillage du FAN en fonction du régime du corps BP et des systèmes variables pilotés par la régulation sont déterminants dans l'obtention d'un modèle théorique (moteur + régulation) de haute qualité.
Correction d'humidité
La présence de vapeur d'eau dans l'air modifie les performances du moteur du fait de la différence de chaleur spécifique entre un air sec et un air chargé en vapeur d'eau ce qui nécessite de corriger les performances du jour de l'essai afin de les ramener en air sec.
Les corrections à appliquer sur les paramètres de poussée, de régimes, de débit carburant et d'EGT sont déterminées à partir d'un modèle moteur dont on fait varier la richesse en vapeur d'eau, de 0 % jusqu'à la saturation, en gardant constante la température d'entrée et la puissance moteur. Par balayages successifs des différents points de régimes du moteur et de température d'entrée que l'on peut rencontrer en essai réel on détermine les différents facteurs de correction qui seront apportés aux paramètres moteurs en fonction du taux d'humidité qui sera mesuré pendant l'essai réel.
Correction de condensation
En fonction de la température ambiante et du degré d'humidité le jour de l'essai du moteur, la manche d'entrée peut être le siège d'une condensation lorsque localement la pression partielle de la vapeur d'eau devient inférieure à la pression de vapeur saturante : le phénomène est exothermique, l'eau cède de la chaleur et donc l'air ambiant voit sa température augmenter. À l'entrée dans le FAN il y a compression donc élévation de température et évaporation ce qui prélève de l'énergie au moteur. Ce prélèvement d'énergie doit être compensé par des correctifs qui ne portent que sur le régime du corps BP.
Correction d'installation d'essais
Correction de banc d'essai
Les essais de moteur qui se font à proximité de zones habitées génèrent une pollution acoustique du même ordre que les zones d'approche d'aéroport. La législation imposant de limiter fortement les nuisances sonores oblige les fabricants de moteur à réaction à réaliser leurs essais en banc fermé. Le bruit est alors limité par leur configuration aérodynamique qui canalise les flux d'entrée d'air et d'éjection à travers des tunnels équipés de traitements acoustiques des parois et présentant des configurations d'entrée et de sortie verticales. Malheureusement la poussée du moteur n'est plus exactement la même que dans un banc d'essai à l'air libre pour un débit carburant identique car le débit d'air supplémentaire à entrainer, lié à l'effet venturi du collecteur de gaz de la cheminée d'échappement, demande de l'énergie au moteur et le résultat final doit être corrigé par calcul pour obtenir la poussée réelle du moteur. Les correctifs apportés sont de l'ordre de 3 % à 10 % suivant les installations.
Les débits d'air à l'entrée des moteurs peuvent varier de 80 kg/s pour les moteurs militaires à 1 600 kg/s pour les moteurs subsoniques de forte poussée ce qui engendre des débits induits très variables en fonction des essais.
Un facteur correctif est alors déterminé pour chaque banc d'essai fermé en évaluant les écarts de performances donnés avec un banc d'essai à l'air libre en utilisant les moteurs de référence ayant servi dans tous les essais de certification. Ce facteur correctif est alors appliqué pour chaque moteur de série passé au banc d'essai fermé. La phase d'essais permettant de déterminer ce facteur correctif s'appelle la « corrélation de banc d'essai ». Cette phase de corrélation n'est obligatoire que dans le cas où l'aérodynamique interne du banc d'essai viendrait à être modifiée de manière significative.
Correction d'instrumentation d'essais
Les installations de mesure et de contrôle d'essai induisent des écarts dans la réponse du moteur et doivent être corrigés dans les résultats finaux pour obtenir les performances réelles du moteur. Les facteurs correctifs à appliquer sur les résultats d'essais sont déterminés par calcul à partir d'un modèle moteur dont on simule le fonctionnement avec et sans instrumentation.
Corrélation de nacelle
Les nacelles utilisées pour les essais de production doivent être comparées à celles utilisées pour les essais au sol des moteurs de démonstration ayant servi aux essais de certification. Les écarts constatés à la suite d'essais menés comparativement se traduisent par des facteurs correctifs que l'on applique aux résultats d'essais de chaque moteur de série.
Dérive de performances des bancs d'essai
Pour déterminer une dérive lente des installations d'essai, on détermine un coefficient de suivi faisant intervenir les températures d'entrée et de sortie du banc ainsi que le carburant consommé lors de l'essai. On établit alors la quantité de travail fournie et, si elle est stable, cela veut dire que le banc d'essai n'évolue pas.
Calculs à régime de référence
Une fois toutes les corrections d'installation réalisées, il faut ajuster les paramètres moteur contractuels pour chaque point d'essai par rapport au régime BP contractuel vendu à l'avionneur. On utilise alors les tables d'interpolation établies lors des essais au sol des moteurs de démonstration pendant la phase de certification.
Les paramètres concernés sont la poussée, le débit carburant, la température EGT et le régime HP pour les double-corps.
Calculs à poussée de référence
Le principe est le même que pour se ramener à régime de référence, mais seul le débit carburant est concerné (utile au calcul de la SFC)
Déroulement d'un essai moteur
Chronologie des opérations
Les opérations devant être réalisées pour passer un moteur au banc d'essai sont les suivantes dans l'ordre chronologique :
- Instrumentation et alimentation en huile puis installation à son point fixe
- Ventilation sèche sans carburant
- Démarrage puis Rodage
- Réglages et contrôles
- Relevé des courbes de performances
- Protection contre la corrosion et arrêt
Suivi de l'essai
Durant l'essai du moteur, le personnel responsable doit :
- surveiller les paramètres à limite de sécurité
- Régimes
- Température turbine
- Vibration
- Températures des paliers d'arbres
- Pression d'huile et de carburant
- vérifier tous les modes de fonctionnement du moteur et contrôler tous les paramètres à tolérance
- contrôler les performances en régimes stabilisés et transitoires
- assurer les contrôles de fin d'essai
- niveau huile
- étanchéité
- témoins d'usure
- délivrer la sanction finale sous forme d'un procès-verbal qui sera remis au client et servira de preuve en cas d'usure prématurée du moteur une fois celui-ci avionné (garantie constructeur).
En cas d'anomalie le moteur n'est pas livré au client et part sur une chaîne hôpital afin d'être expertisé ; le retour en essai de production se fera après traitement complet du problème.
Exploitation et maintenance
Une fois le moteur vendu et réceptionné par l'exploitant, sa vie opérationnelle commence et sera ponctuée d'opérations de maintenance préventive et curative légères sous l'aile ainsi que d'opérations de maintenance lourde en atelier afin de permettre une durée d'utilisation de plusieurs dizaines d'années.
Notions générales
Voici quelques définitions sur certains concepts liés à l'exploitation des moteurs
Efficacités et coûts
L'efficacité regroupe la qualité intrinsèque du matériel et le coût de possession qui comprend :
- le coût initial d'acquisition
- le coût d'exploitation
- le coût de maintenance
Sûreté et sécurité
La sûreté exprime l'aptitude d'un matériel à assurer son fonctionnement nominal. La sécurité est l'aptitude d'un matériel à ne pas occasionner de dommages aux personnes.
Disponibilité
La disponibilité (D) exprime le fait qu'un matériel est en mesure, à un moment donné, d'assurer toutes les fonctions pour lesquelles il a été conçu. On distingue la disponibilité apparente et la disponibilité réelle. Comme le contrôle total de la disponibilité est généralement impossible, seule la disponibilité apparente est accessible.
L'évaluation de la disponibilité peut se faire en considérant la moyenne des temps de bon fonctionnement (MTBF : Mean Time Between Failure) et la moyenne des temps nécessaires aux réparations (MTTR : Mean Time To Repair).

On peut donc obtenir la disponibilité par la fiabilité et par les moyens mis en œuvre pour réparer le matériel.
Fiabilité
La fiabilité est l'aptitude d'un matériel à accomplir une fonction déterminée dans des conditions données, pour une période déterminée. C'est en fait la probabilité de fonctionnement sans panne. Pour la définir, on distingue le taux d'avarie L (Lambda) et le MTBF (Mean Time Between Failure). Le taux d'avarie L est le pourcentage d'échantillons de la population N tombant en panne pendant le temps unité x.

avec N1 = Echantillons à l'instant t et N2 = Echantillons à l'instant (t + x)
Le MTBF est l'inverse du taux d'avarie :

On exprime souvent la fiabilité en nombre de pannes par heure, par exemple 1.10-6 ce qui signifie que la panne intervient au bout de 1 million d'heures de fonctionnement.
Le taux d'avarie du matériel évolue dans le temps que ce soit pour des organes mécaniques ou électroniques, suivant trois périodes distinctes :
- Une première période assez courte où le matériel souffre de pannes de jeunesse
- Une deuxième période plus longue où le taux d'avarie est le plus faible,
- Une troisième période très courte dite de "vieillesse" où le taux d'avarie augmente de façon notable.
Maintenabilité
La maintenabilité est l'aptitude d'un matériel à être maintenu en état de fonctionnement. Les constituants de la maintenabilité (exploitation, fiabilité, démontabilité, testabilité...) sont en général déterminés lors de la phase de conception du matériel.
Maintenance On peut définir la maintenance comme l'ensemble des moyens et actions nécessaires pour "maintenir" le matériel en service.
La dépose d'un moteur, module ou accessoire majeur peut être justifiée par 3 limites :
- le potentiel entre révisions
- la limite de vie de certaines pièces en cycle
- le potentiel calendaire.
Potentiel
Le potentiel entre révisions (en anglais : TBO = Time Between Overhaul) est la durée d'utilisation autorisée avant qu'une révision générale ne s'impose sur un moteur, un module ou un accessoire majeur.
Le potentiel d'un moteur ou d'un module est déterminé en fonction d'essais justificatifs et de l'expérience acquise. Il est généralement exprimé en heures de fonctionnement, mais aussi en année pour les potentiels calendaires existant pour ces mêmes éléments.
Le potentiel peut être l'objet d'un programme d'extension fondé sur l'expertise des moteurs arrivant en fin de potentiel.
Limites calendères
C'est la durée maxi disponible après la remise en service sur aéronef consécutive à une révision générale ou réparation majeure.
Limites d'utilisations
Pour certains éléments (ex : Roulements ou pignons), il existe une limite d'utilisation exprimée en heures ou cycle indépendante du potentiel moteur.
Compteur de Potentiel
Sur certains moteurs équipés de calculateur de régulation et et de surveillance, une fonction de comptage de potentiel est disponible. Cette fonction prend en considération les régimes et température turbine du moteur durant son fonctionnement sous l'aile afin de calculer les taux de fatigue sur les ensembles tournants.
Durée de vie limitée
Certains éléments du moteur ont une durée d'utilisation autorisée avant leur retrait du service. cette durée de vie est déterminée par des calculs et des essais justificatifs. Elle est exprimée en nombre d'heures de fonctionnement et en cycles (1 cycle = 1 démarrage, 1 mise en puissance, 1 arrêt).
Bulletins de service
Toutes les modifications apportées au matériel sont classées selon les modalités d'application et le degré d'urgence. Ces modifications peuvent être facultatives, recommandées ou impératives. Toute modification fait l'objet de bulletins de service émis par le constructeur et approuvés par les Services Officiels de l'aéronautique.
Exploitation
En exploitation des procédures de conduite du moteur sont mises en œuvre par les compagnies aériennes sur recommandations des constructeurs afin de permettre une dégradation minimum des performances pour que les opérations de maintenance à mettre en œuvre soient minimisées sur une période d'exploitation donnée. Un suivit en temps réel des performances du moteur est assuré par le traitement des données émises par l'aéronef durant chacun de ses vols. Un certain nombre de limitations, qui pour certaines sont spécifiques à chaque type de moteur, imposent le suivit opérationnel et le changement de certaines pièces à durée de vie limitée.
Procédures de conduite
Les procédures de conduite du moteur sont définies par une documentation officielle (manuel d'utilisation, manuel de vol...). On distingue les procédures de conduite dites normales et celles de secours.
Les procédures normales définissent les actions de conduite pour les différentes phases de fonctionnement : démarrage, mise en puissance, conduite en vol, arrêt moteur, rallumage, ventilation...
Les procédures de secours définissent les actions de conduite dans des conditions exceptionnelles : arrêt moteur en vol, pannes de systèmes, incendie...
Gestion de la poussée
Tous les avions de transport commerciaux sont construit avec une motorisation présentant une marge de poussée excédentaire permettant de satisfaire aux obligations de certification. L'avionneur et le motoriste réalise un ensemble avion plus motorisation pour les plus sévères conditions ( charge maxi, jour chaud, haute altitude, etc ..) pouvant être rencontrées dans les missions qui lui seront attribuées.
De ce fait dans la plupart des conditions d'utilisation de l'avion il existera une importante réserve de poussée qu'il ne sera pas utile d'utiliser. Sachant que cette réserve peut atteindre plus de 25% de la poussée max disponible en fonction des conditions de décollage (Take Off) et que l'exploitation à la poussée maximum a un impact directe sur la détérioration des performances et la durée de vie sous l'aile il est nécessaire de faire une gestion optimum (en fonction du besoin) de la poussée demandée aux moteurs.
La corrélation entre détérioration des performances et optimisation de l'utilisation de la poussée ayant été mise en évidence de manière statistique sur une flotte importante de moteurs il est apparu évident que la gestion de l'utilisation de la poussée d'un moteur était primordiale dans la maîtrise de la détérioration des performances de celui-ci.
Limitations
Un moteur est conçu pour fonctionner à l'intérieur de certaines limites déterminées par le constructeur : domaine de vol, vitesses, températures, pressions, facteurs de charge, temps...
- Domaine de vol
Le moteur est conçu pour fonctionner dans un domaine déterminé de pression et de température extérieure correspondant à ses futures missions opérationnelles.
- Domaine de rallumage
Le rallumage en vol suite à une extinction n'est possible que dans certaines conditions de vol (altitude, vitesse...).
- Régimes de fonctionnement
Les régimes des différentes pièces tournantes du moteur font l'objet de limites en amplitude et en durée afin de protéger l'intégrité de la machine et de permettre une durée de vie sous l'aile compatible avec l'exploitation.
- Température des gaz
Les limites sont imposées par la résistance des parties chaudes et notamment celles des aubes de turbine. Il peut y avoir plusieurs limites : température résiduelle avant démarrage, température maxi lors du démarrage, températures maxi en vol...
- Limites de circuit d'huile
Elles sont représentées par les limites de pression, température et consommation ; exemples : pression d'huile maxi, pression d'huile mini, température d'huile maxi, température d'huile mini pour démarrer, consommation d'huile maxi...
- Limites de circuit carburant
Elles sont en général représentées par les limites de température mini et maxi et dans certains cas par les limites de pression...
- Limites électriques
Limites de tension des circuits, limites de consommation, limites de prélèvements...
- Limites de démarrage
Un certain nombre de limites sont associées au démarrage du moteur : domaine de démarrage, limites des paramètres (températures, vitesses...) et limites en temps (temps de démarrage, temps maxi de ventilation, temps de stabilisation avant l'arrêt, temps d'autorotation lors de l'arrêt...).
- Limites diverses
limite de prélèvement d'air, limites de vibrations, limites de facteurs de charge...
Maintenance
Généralités
On peut distinguer trois modes de maintenance :
- maintenance avec temps limite
- maintenance selon l'état
- maintenance avec surveillance de comportement.
Le choix d'appliquer l'un ou l'autre de ces modes à un ou plusieurs éléments du moteur résulte de l'analyse préalable des fonctions principales du moteur, des résultats obtenus dans les études de fiabilité, d'essais particuliers et aussi de l'expérience acquise dans la vie opérationnelle.
Les opérations de maintenance sont décrites dans la documentation relative au moteur :
- Manuel de Maintenance,
- Instruction Technique de maintenance
- Manuel de révision (réparation).
Maintenance avec temps limite
Dans ce mode de maintenance, les éléments sont déposés à échéance fixe et révisés si il leur reste du potentiel de vie ou retirés du service en cas d'atteinte de la limite de durée de vie.
Maintenance selon l'état
Cela consiste à effectuer les procédures de maintenance selon l'état des éléments et donc de surveiller la dégradation des pièces concernées afin de déterminer une intervention en regard du défaut constaté. Cela fait appel à des moyens de surveillance comme l'analyse chimique de l'huile ou le contrôle visuel par une méthode endoscopique...
Maintenance avec surveillance de comportement
Ce type de maintenance est basée sur la surveillance permanente de certains paramètres significatifs du fonctionnement du moteur afin de permettre la détection anticipée des anomalies et d'appliquer les procédures de maintenance adéquates avant que la défaillance n'apparaisse.
Echelons de maintenance
la maintenance a été décomposée en plusieurs échelons déterminés en fonction des difficultés d'intervention, du temps nécessaire pour effectuer l'intervention et de considérations logistiques et législatives. Un exemple courant de répartition des niveaux est le suivant :
- 1er Echelon : Moteur monté sur l'aéronef (Visites, dépose LRU...)
- 2e Echelon : Moteur déposé de l'aéronef (Dépose - Pose SRU et modules)
- 3e Echelon : Moteur déposé et Maintenance lourde (Intervention sur les modules...)
- 4e Echelon : Révision générale - Réparation (Atelier spécialisé) - passage au banc d'essais avant repose sous l'aile
Types de maintenance
On distingue principalement deux types de maintenance :
- les opérations de maintenance dites préventives
- les opérations dites correctives
Maintenance préventive
La maintenance préventive comprend les procédures qui doivent être effectuées systématiquement afin de maintenir le moteur en service dans des conditions optimales de sécurité. Le programme de maintenance comprend les procédures dites de mise en œuvre telles que
- les visites avant vol
- les visites après vol
- les visites dites périodiques de période (50, 100, 400 heures).
Maintenance corrective
La maintenance corrective comprend toutes les procédures devant être réalisées en cas d'incident, panne, défaut... Les actions correctives doivent permettre de remettre le moteur en service normal le plus rapidement possible. La maintenance corrective recouvre : le diagnostic de panne, les contrôles fonctionnels, les contrôles d'état, les déposes et poses d'éléments, les réglages...
Procédures de maintenance
Les procédures de maintenance qui sont spécifiques à chaque moteur présentent certaines parties communes telles que :
- les visites techniques courantes
- les contrôles et procédures diverses
- les déposes et reposes de modules ou d'éléments
- les réglages effectués en statique ou en dynamique au banc d'essais ou sous l'aile.
Mise en œuvre des procédures de maintenance
On peut mentionner les précautions d'usage telles que:
- le respect des zones dangereuses,
- les mesures à prendre en cas d'incendie,
- la position de l'appareil (par rapport au vent et aux installations avoisinantes)
- la zone d'aspiration
- etc..
Les Visites de mise en œuvre
Elles sont comprises dans le programme d'entretien courant. On distingue :
- la visite avant vol
- la visite après vol
- la visite après le dernier vol de la journée...
En général, elles se bornent à des inspections visuelles, en particulier de l'entrée d'air et de l'échappement. Elles se déroulent selon un cheminement particulier permettant de vérifier le maximum d'éléments de façon rationnelle.
Le Point fixe de contrôle
Ce point fixe est effectué moteur sous l'aile. Il a pour objet le contrôle des performances et de l'intégrité mécanique du moteur. Il est effectué à intervalles réguliers ou après échange d'éléments ou suite à une analyse de panne. Dans certains cas, il est complété par un ou plusieurs essais en vol. Pour des raisons économiques, on cherche à réduire la durée et le nombre de points fixes. Lors d'un point fixe, les précautions classiques de mise en œuvre doivent être prises ; les différents paramètres moteurs servant à apprécier l'état du moteur sont relevés et consignés sur une fiche prévue à cet effet.
Visites périodiques
Ce sont des visites d'entretien devant être effectuées à intervalles réguliers. Elles comprennent un certain nombre d'interventions telles que :
- les inspections visuelles
- La visites des filtres et des bouchons magnétiques sur le circuit d'huile
- Les prélèvements d'huile pour analyse chimique et spectrographique
Une visite périodique est généralement complétée par un point fixe. Leur périodicité qui est fonction du matériel est de quelques heures ou dizaines d'heures (exemple : visite 25 - 50 - 100 - 300 heures). Les visites peuvent être réalisées de façon "bloquée" ou "étalée".
Les visites dites "bloquées" correspondent à l'exécution de l'ensemble des opérations d'un type de visite à l'échéance indiquée. Dans le cas de "visites étalées" (ou progressives), l'appareil n'est pas immobilisé à échéances fixes. On profite des périodes de non-activité pour effectuer progressivement la totalité des opérations en respectant, néanmoins, la période pour chaque type d'intervention. Le choix de la méthode d'entretien (bloquée ou progressive) est laissé à l'initiative de l'utilisateur selon des critères qui lui sont propres.
La liste suivante non exhaustive donne une idée de ce qui peut être réalisé :
- Vérifications visuelles d'état : entrée d'air, compresseur, tuyère, fixations câblages, commandes,
- Vérifications fonctionnelles,
- Inspection des filtres (indicateur colmatage, éléments....), - Inspection des bouchons magnétiques,
- Prélèvement d'huile pour analyse,
- Point fixe de contrôle (paramètres...),
- Niveaux - Pleins éventuels,
- Endoscopie, vibrations..
Contrôles
L'activité de maintenance est aussi caractérisée par de nombreux contrôles fonctionnels ou d'états.
Ci-après, la liste de quelques contrôles types :
- Contrôle de puissance moteur (Power Assurance Check)
- Contrôle manuel de la libre rotation de l'ensemble tournant pour vérification de l'absence de frictions anormales
- Contrôle du temps d'autorotation (temps pour l'arrêt complet de l'ensemble tournant lors de l'arrêt moteur)
- Contrôle du jeu en bout de pales turbine
- Contrôle visuel de l'érosion compresseur avec outillage
- Contrôle visuel direct (entrée d'air, échappement, carters, liaisons, freinages, tuyauteries, accessoires...)
- Contrôle endoscopique de l'état des pièces internes
- Contrôle des jeux
- Contrôle des vibrations
- Contrôle de perméabilité (écoulement à travers certains éléments)
- Contrôle de fuites
- Contrôle et détection de criques
- Contrôles fonctionnels divers (utilisation d'outillage de tests).
Stockage
Lorsque, pour une raison quelconque, le moteur ne doit pas fonctionner pendant une certaine période, il faut le protéger contre la corrosion en appliquant une procédure dite de stockage. Cette procédure est fonction de la position du moteur (installé sur avion ou non) et de la durée d'immobilisation prévue. D'une manière générale, elle consiste à faire fonctionner le moteur avec un mélange de carburant et d'huile tout en pulvérisant de l'huile de stockage dans l'entrée d'air. À l'issue de ce point fixe de stockage, tous les orifices sont obstrués et le moteur protégé par un moyen quelconque (bâches, capots...).
Pour les immobilisations de longue durée ou le transport, le moteur est déposé et placé dans un container spécial souvent pressurisé et muni de produits déshydratants. Le contrôle périodique du stockage est prévu dans les notices d'entretien. Note : En ce qui concerne le transport, des précautions doivent être prises pour ne pas détériorer les moteurs par chocs, ou vibrations excessives.
Lavage compresseur
Parmi les causes de déposes prématurées d'un moteur, celles dues à la détérioration du compresseur par érosion ou corrosion sont relativement fréquentes. En effet, la veine d'air (en particulier le compresseur) travaille avec de l'air pouvant être chargé d'éléments érosifs ou corrosifs. Par exemple, érosion en atmosphère sablonneuse, corrosion en atmosphère saline. De plus, l'amalgame avec des fuites éventuelles provoque un encrassement qui diminue les performances.
Pour effectuer un lavage moteur on pulvérise un mélange d'eau avec un produit de nettoyage dans l'entrée d'air. Ces procédures de nettoyage s'appliquent soit en prévention soit une fois détecter une baisse de performances lors du suivit moteur sous l'aile.
Le manuel d'entretien moteur comporte toutes les indications nécessaires pour effectuer ces opérations de maintenance qui, rappelons le, sont d'une grande importance pour éviter le déroulement, souvent irréversible, du processus (d'encrassement ou de corrosions).
Procédure en cas d'ingestion de corps étrangers
Que ce soit en vol ou au sol, un moteur peut absorber dans le débit d'air différents objets pouvant détériorer les aubes de compresseur et de turbine. Le moteur est certifié pour tenir en cas d'injection de volatiles calibrés, de petits grêlons ou d'eau lors des phases de décollage et d'atterrissage.
Au sol, il s'agit le plus souvent d'objets laissés à proximité de l'entrée d'air et en vol, il s'agit le plus souvent de la rencontre avec des oiseaux. L'ingestion de corps étrangers peut entraîner des détériorations plus ou moins graves pouvant se traduire par des vibrations importantes, une baisse de performance et même l'arrêt du moteur.
Lorsqu'une ingestion est observée, il convient de contrôler la veine d'air et en particulier les aubes du (des) compresseur(s) et de la (des) turbine(s). La solution d'entretien dépend ensuite du degré d'anomalie et du type de moteur.
Procédures de déposes et de poses
Parmi les éléments du moteur qui peuvent être remplacés il y a ceux qui sont remplaçables en ligne (sous l'aile) et ceux qui ne sont remplaçables qu'en atelier après dépose du moteur.
Les premiers sont l'objet des procédures pour LRU (Line Replacable Unit) et les seconds des procédures pour SRU (Shop Replacable Unit).
Modularité
La modularité (conception modulaire) permet de constituer un moteur d'éléments parfaitement interchangeables appelés Modules afin de simplifier les opérations de maintenance sur une flotte de moteurs identiques.
La modularité permet une plus grande disponibilité opérationnelle et une réduction importante du coût d'entretien.
Avec la conception modulaire la notion de potentiel moteur évolue pour être remplacée par celle de limites propres à chaque module.
La séparation en modules pré-équilibrés et pré-réglés implique une gestion plus lourde mais donne la possibilité pour certains modules d'un remplacement sans retour du moteur complet en usine.
Réglages
Un moteur doit subir un certains nombre de vérifications avant montage sous l'aile et être Bon de vol. Ceci est encore plus vrai lorsque celui ci sort d'une opération de maintenance et donc les constructeurs avec l'apparition des nouvelles régulation de type FADEC en on profité pour intégrer un certains nombre de fonctions permettant de simplifier considérablement les réglages de mise au point.
Dépannage
Le dépannage est guidé par deux impératifs qui sont le temps d'immobilisation du moteur et la dépose "justifiée" d'éléments. La procédure de dépannage va dépendre de l'anomalie et il est difficile de donner une méthode pouvant s'appliquer à tous les cas. Néanmoins, on peut dire que la connaissance du matériel (connaissance de la constitution, du fonctionnement et du comportement) et une recherche méthodique concourent à un diagnostic sûr et un dépannage rapide.
Le principe général consiste à définir clairement le symptôme, à l'interpréter et à procéder au diagnostic de façon logique afin de choisir et d'appliquer la procédure permettant le dépannage.
La procédure choisie peut être :
- un réglage
- le démontage, nettoyage, remontage d'un filtre colmaté
- le changement d'une pièce défectueuse ou en fin de vie
- la vérification fonctionnelle du moteur (point fixe)
- etc.
Le manuel d'entretien comporte des tableaux de recherche de panne qui répertories les cas de défaillance les plus courants pouvant être rencontrés mais la connaissance du fonctionnement du moteur reste indispensable dans la plupart des cas.
Moyens de maintenance
Les moyens utilisés pour effectuer la maintenance sont très diversifiés et les suivants font partie des principaux :
- l'analyse d'huile
- le contrôle des vibrations
- le contrôle endoscopique
- la radiographie
L'analyse d'huile
Le circuit d'huile de lubrification est muni de filtres et de bouchons magnétiques qui retiennent certaines particules en suspension. Cependant, l'huile se charge aussi de petites particules qui ne peuvent être retenues par ces moyens classiques, mais qui peuvent être détectées et mesurées par l'analyse spectrométrique de l'huile. Les résultats d'une telle analyse permettent de déceler à l'avance les défaillances potentielles et les usures anormales.
Principe de l'analyse spectrométrique
Le principe de base est d'observer le rapport entre la vitesse d'usure des pièces et la vitesse de pollution de l'huile car plus la vitesse de pollution est élevée, plus la perte de métal est importante et, par conséquent, plus grand est le risque de rupture. Le paramètre déterminant est donc, non seulement la concentration mesurée à un instant donné, mais aussi et surtout l'accroissement de la vitesse de pollution.
Le spectromètre qui se compose de deux électrodes, une fixe et une tournant dans l'huile à analyser permet grâce à la différence de potentiel entre les deux électrodes de vaporiser l'huile ce qui libère des électrons provoquant une onde lumineuse captée par un système optique qui la diffracte en rayons élémentaires correspondant au métal utilisé.
Principe de Ferrographie
C'est une technique de laboratoire qui permet de séparer les particules contenues dans un échantillon d'huile par action d'un champ magnétique puissant.
ces particules sont ensuite soumises à diverses procédures :
- Examen des particules (visuel ou/et microscopique)
- Comptage par taille (manuel ou automatique)
- Analyse après mise en température
À partir des indications fournies, on peut arriver à définir l'élément en cause et le mode d'usure rencontré. On obtient ainsi des résultats intéressants dans le domaine de survie des roulements (criques de fatigue qui génèrent des éclats de forme sphérique).
Efficacité des différentes méthodes
Ces méthodes sont complémentaires et il est souvent nécessaire de les utiliser conjointement pour obtenir une surveillance parfaite d'un matériel donné. Les modes d'usure différents génèrent des particules de taille et de forme différentes, et chaque méthode a une efficacité maximum pour certaines grosseurs de particules : par exemple l'analyse spectro n'est efficace que pour les particules inférieures à 15 microns, le bouchon magnétique est particulièrement adapté aux particules de 100 à 300 microns. Un des gros intérêts de la ferrographie est de venir combler le trou existant entre ces 2 méthodes, en permettant de recueillir et d'analyser les particules de 15 à 100 microns.
Ces méthodes, parfois très sophistiquées, ne doivent pas faire oublier les moyens d'évaluations traditionnels réalisés "in situ". Il s'agit là des procédures de maintenance courantes faisant appel à la surveillance et à l'expérience du mécanicien :
- Examen des filtres
- Examen des bouchons magnétiques
- Vérification de l'huile (couleur, odeur...)
- Vérification des jeux
- Vérification des bruits (bruits anormaux)
- Vérifications visuelles diverses
Contrôle des vibrations
Compte tenu des vitesses de rotation élevées, tout déséquilibre de l'ensemble tournant peut, s'il dépasse un certain seuil, avoir des conséquences fâcheuses en raison des vibrations engendrées. Il convient de s'assurer que ces limites ne sont pas dépassées lors du fonctionnement.
Toute déformation ou détérioration de l'ensemble tournant se traduisant par des vibrations, la surveillance de l'amplitude de ces vibrations peut permettre la détection anticipée d'une anomalie. La mesure de vibration s'effectue à l'aide de capteurs placés au voisinage de l'ensemble à contrôler. Les capteurs utilisés sont de type électromagnétique ou piézo- électrique.
Le motoriste définit les valeurs limites et les actions à entreprendre (échange de palier, ragréage de rotor ou même échange du moteur complet).
Contrôle endoscopique
Le contrôle endoscopique permet l'examen visuel des pièces internes à travers de petits orifices sans procéder au démontage.
Principe de l'endoscope
Il se compose d'une canne munie de fibres optiques qui conduisent la lumière et d'un système de vision constitué de lentilles. La lumière issue d'un générateur est froide et anti-déflagrante, ce qui permet les contrôles en milieu détonant.
Pour le contrôle, la canne est introduite par des orifices prévus à cet effet en différents points du moteur. Le déplacement et l'orientation de la canne permettent l'observation de la pièce complète.
Contrôle radiographique
La radiographie peut être utilisée comme moyen de contrôle non destructif et le procédé envisagé, de type gammagraphique, permet l'inspection sans effectuer de dépose.
La gammagraphie combine l'utilisation de la radioactivité et de la photographie. Une source de rayons γ traverse la pièce à examiner qui absorbe une partie du rayonnement. Le rayonnement résultant impressionne le film photographique faisant apparaître les défauts de la pièce.
Notes et références
- ↑ Brevet de Maxime Guillaume, numéro 534 801.
- ↑ « Brevet d'invention - Propulseur par réaction sur air », sur Office national de la propriété industrielle
- 1 2 3 (en) Kendall F. Haven (2006), 100 greatest science inventions of all time, How was the jet engine invented ?, p. 225-226
- 1 2 3 4 (en) Mary Bellis, « Jet Engines - Hans von Ohain and Sir Frank Whittle - The History of the Jet Engine », sur About.com (consulté le 16 août 2009), p. 1
- ↑ (en) « Junkers Jumo 004 B4 Turbojet Engine », sur National Air and Space Museum (consulté le 16 août 2009)
- 1 2 3 (en) Klaus Hünecke (1997), Jet engines : fundamentals of theory, design and operation, Turbine Aircraft Engine, chap. 1, p. 3
- ↑ (en) « History of Jet Engines », sur Scientists and Friends (consulté le 16 août 2009), p. 1 à 5
- ↑ « Bell P-59 Airacomet : le faux premier jet de l'USAAF », sur Avion légendaire (consulté le 25 août 2009)
- ↑ « Ryan FR-1 Fireball : le chasseur hybride de l'US Navy », sur Avion légendaire (consulté le 25 août 2009)
- ↑ « Nord N.1500 Griffon : un statoréacteur français trop en avance », sur Avion légendaire (consulté le 25 août 2009)
- ↑ (en) « McDonnell F-4A Phantom II "Sageburner" », sur National Air and Space Museum (consulté le 16 août 2009)
- ↑ (en) « De Havilland Comet », sur Century of flight (consulté le 16 août 2009)
- 1 2 3 4 5 6 7 8 Jean-Claude Thevenin (2004), Le turboréacteur, le moteur des avions à réaction, chap. 6 - Quelques chiffres caractéristiques, p. 38-40
- 1 2 (en) « How a Jet Engine Works ? », sur About.com (consulté le 16 août 2009)
- ↑ « Microturbo - Groupe Safran », sur microturbo.com (consulté le 25 août 2009)
- 1 2 Jean-Claude Thevenin (2004), Le turboréacteur, le moteur des avions à réaction, chap. 2 - Les différents types de propulseurs et leur poussée, p. 8
- 1 2 Jean-Claude Thevenin (2004), Le turboréacteur, le moteur des avions à réaction, chap. 5 - Les matériaux, la conception mécanique et la fabrication des turboréacteurs, p. 32-34
- 1 2 « Étude du bruit d'un turboréacteur » (consulté le 30 août 2009)
- ↑ « Simulation numérique des écoulements et aéroacoustique », sur ONERA (consulté le 30 août 2009)
- ↑ « bruit aval de soufflante d'un turboréacteur double-flux », sur ONERA (consulté le 30 août 2009)
- ↑ « L'environnement - Pollution » [PDF], sur ACIPA (consulté le 30 août 2009)
- 1 2 3 4 Jean-Claude Thevenin (2004), Le turboréacteur, le moteur des avions à réaction, chap. 3 - Le principe de fonctionnement du turboréacteur, p. 12-15
- ↑ « Réacteur Goblin », sur La Force Aérienne du Canada (consulté le 24 août 2009)
- ↑ Patrice Guerre-Berthelot, 70 ans d'avions à réaction, Marines éditions), (ISBN 978-2-35743-062-4), p. 22
- 1 2 3 « Le système propulsif d'un aéronef » (consulté le 18 août 2009)
- 1 2 3 4 « Turbofan » (consulté le 18 août 2009)
- ↑ Jean-Claude Thevenin (2004), Le turboréacteur, le moteur des avions à réaction, Chap. 3 - Le principe de fonctionnement du turboréacteur, p. 25
- ↑ Jean-Claude Thevenin (2004), Le turboréacteur, le moteur des avions à réaction, chap. 3 - Le principe de fonctionnement du turboréacteur, p. 26
- 1 2 (en) « How does an afterburner work ? », sur How stuff works ? (consulté le 15 août 2009)
- ↑ « Systèmes de commande d’inverseurs de poussée », sur Messier Bugatti (consulté le 19 août 2009)
- 1 2 « La Poussée Vectorielle », sur Avion légendaire.net (consulté le 19 août 2009)
- 1 2 (en) « Auxiliary Power Units », sur NASA (consulté le 19 août 2009)
- ↑ Thrust SSC, Sport Auto, numéro 430, novembre 1997, p. 10-11
- 1 2 « Avions de plus de 150 places : qui motorise quoi ? », Air&Cosmos, no 2176S, , p. 102
Annexes
Bibliographie
- R. Kling, Thermodynamique générale et applications, Paris, Éditions Technip, (OCLC 19286332)
- R. Ouziaux & J. Perrier, Mécanique appliquée, Tome 1, Mécanique des fluides, Dunod,
- R. Ouziaux & J. Perrier, Mécanique appliquée, Tome 2, Thermodynamique, Dunod,
- Jacques Lachnitt, La mécanique des fluides, PUF que sais-je ?
- R. Comolet, Mécanique expérimentale des fluides,Tomes 1, 2 et 3, Masson,
- G. Lemasson, Les machines transformatrices d'énergie, Delagrave,
- R. Vichnievsky, Thermodynamique appliquée aux machines, Masson,
- V. Bensimhon, Fonctionnement hors adaptation des Turbomachines, Masson,
- (en) Kendall F. Haven, 100 greatest science inventions of all time, Libraries Unlimited, , 333 p. (ISBN 978-1591582649, lire en ligne)
- (en) Klaus Hünecke, Jet engines : fundamentals of theory, design, and operation, Zenith Imprint, , 241 p. (ISBN 978-0760304594, lire en ligne)
- Jean-Claude Thevenin, Le turboréacteur, moteur des avions à réaction, Association Aéronautique et Astronautique de France, , 46 p. (lire en ligne)
- Serge Boudigues, Les turboréacteurs, Dunod, , 112 p.
- Gilbert Klopfstein, Comprendre l'avion(Tome 3), Cépaduès, , 256 p.
- J. Découflet, Aérothermodynamique des turbomachines, cours ENSAE
- Alfred Bodemer, Les turbomachines aéronautiques mondiales, Paris, éditions Larivière, coll. « Docavia » (no 10), , 255 p. (OCLC 37145469)
- Alfred Bodemer et Robert Laugier, L'ATAR et tous les autres moteurs à réaction français, Riquewihr, Éditions J.D. Reiber, , 335 p. (ISBN 978-2-951-07450-7, OCLC 41516392)
- Lehmann et Lepourry, Technologie des Turboréacteurs, Toulouse, ENAC, , 323 p. (OCLC 300314006)
Articles connexes
- Efficacité d'un turboréacteur
- Liste des motoristes aéronautiques par pays
- Nacelle (avion)
Liens externes
- Animation d'un turboréacteur (compresseur centrifuge)
- Portail de l’aéronautique
- Portail de l’énergie